Head safety:
Introduction:
Head injury accident is one kind of the major occupational accidents in work place, particularly in the construction industry. Every year many workers injured or are even killed as a result of head injury. The main risks of head injury in the workplaces are as follows:
- where there is a possibility that a worker may be struck on his head by a falling or flying object;
- where a worker may strike his head against a protruded object or may be struck by a swinging object.
To effectively reduce the risks of head injury,an appropriate type of safety helmets should be provided.The safety helmet selected should satisfy certain performance requirements including shock absorption, resistance to penetration; and be adjustable to fit and make comfortable to the user. certainly, the safety helmet can never be effective unless it is properly worn for the purpose.
The use of safety helmet, like other personal protective equipment, is always regarded as the last resort for accident prevention. In principle, reducing or controlling the risks of injury at source should be considered first. Hazards of job processes or working environments may be the root sources of head injury. Appropriate preventive measures should be taken in order to prevent head injury.Some practical examples are: provision of toe-boards to prevent objects falling from the working platform, erection of catching fans and nets to reduce the likelihood of people being struck by any falling objects, and capping of projections from structures to prevent accidental bumping, etc.
It is crucial that 'safety helmet' is not a substitute for other preventive measures of head injury accidents. Safety helmets do not prevent head injury accidents, but only reduce the severity.
Legal requirements:
Each affected employee shall wear protective helmets when working in areas where there is a potential for injury to the head from falling objects. Protective helmets designed to reduce electrical shock hazard shall be worn by each such affected employee when near exposed electrical conductors which could contact the head.
Although the OSHA standards themselves do not identify specific occupations or applications where head protection is required, there are some examples:
Some examples of occupations for which head protection should be routinely considered are: carpenters, electricians, lineman, mechanics and repairers, plumbers and pipe fitters, assemblers, packers, wrappers, sawyers, welders, labours, freight handlers, timber cutting and logging, stock handlers, and warehouse labours."
The appendix also provides examples of general applications where head protection should be worn.
Helmets must comply with the performance guidelines in the ANSI Z89.1-1986, American National Standard for Personal Protection—Protective Head wear for Industrial Workers Requirements.
Special Requirements: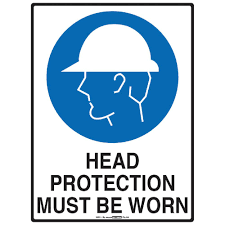
Legal obligation is imposed on the contractor responsible for a construction site under Regulation 48 of the Construction Sites (Safety) Regulations to provide each workman employed on the site with a suitable safety helmet and to ensure that no workman remains on the site unless he is wearing a suitable safety helmet. Besides, no person shall enter a construction site unless he is wearing a suitable safety helmet.
Similar provisions have also been laid down on Regulations (17)(1) and 36(1) of the Quarries (Safety) Regulations (Subsidiary legislation of Chapter 59) requiring proprietors to provide suitable safety helmets and workers to wear the safety helmets provided respectively.
General duties and provisions:
Every employer is required under Section 6 of the Occupational Safety and Health Ordinance to ensure the safety and health at work of his employees. Therefore it is the responsibility of the employer to assess and evaluate the risks of head injury associated with the working environment
and activities to be done;and decide whether safety helmets are needed to be worn.The responsibility extends to include the provision of information, instruction, training and supervision for all persons employed by him. To effectively discharge the duties, the employer should provide a safe system
of work or establish a head protection programme documenting all aspects of selection, use, care and maintenance of safety helmets.
Legal obligation is imposed on every employee under Section 8 of the Occupational Safety and Health Ordinance to take care for the safety and health of others and himself; and to co-operate with his employer to enable safety requirements and rules are complied with. In this respect, he must follow the rules and instructions of his employer to ensure the safety helmet provided is properly worn and taken care of. In case of doubt, advice from his employer should be sought. He should not misuse the helmet and should report any defects immediately.
ANSI Z89.1-1986 separates protective helmets into different types and classes.
The standard identifies Type 1 and Type 2 helmets. Type 1 helmets incorporate a full brim (the brim fully encircles the dome of the hat); Type 2 helmets have no encircling brim, but may include a short bill on the front (similar to a baseball cap).
In terms of electrical performance, ANSI Z89.1-1986 recognizes three classes:
- Class A Helmets are intended to reduce the force of impact of falling objects and to reduce the danger of contact with exposed low-voltage electrical conductors. For certification, sample shells are proof-tested at 2,200 volts of electrical charge.
- Class B Helmets are intended to reduce the force of impact of falling objects and to reduce the danger of contact with exposed high-voltage electrical conductors. Sample shells are proof-tested at 20,000 volts.
- Class C Helmets are intended to reduce the force of impact of falling objects, but offer no electrical protection.
Note: The voltages stated in Classes A and B are not intended to be an indication of the voltage at which the headgear protects the wearer.
In addition to electrical protection, hard hats are also tested for impact and penetration resistance from blows to the top of the head, flammability resistance, and water absorption. The rigorous testing requirements are described in detail within the standard.
Safe system of work:
A safe system of work for head protection or a head protection programme should be provided documenting all aspects of risk assessment, control measures, proper selection, use, care and maintenance of suitable safety helmets, implementation and monitoring. This can provide a systematic and effective approach to ensure the proper use and care of safety helmets as well as the implementation of control measures for eliminating or reducing the hazards associated with head injury. The head protection programme should include but is not limited to the following:
Risk assessment: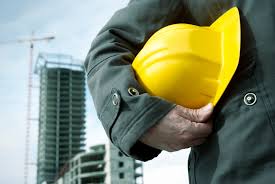
Risk assessment should be conducted to identify the potential hazards of head injury relating to the work to be done and the working environment, and assess the level of the risks associated with each hazard. After the result of risk assessment is documented, engineering or administrative controls
encompassing anticipated changes in the task or process should be considered and documented for elimination or reduction of the risks at source. Furthermore, adequate arrangements on the selection, use, care and maintenance of safety helmets should be incorporated once the need has been identified. It is important to ensure that the roles and responsibilities of individuals are properly
defined and clearly spelled out.
Selection criteria and procedures:
One of the key elements of the head protection programme is the proper selection of safety helmets. Detailed procedures for selecting suitable safety helmets should therefore be documented. First of all, the design and performance criteria appropriate to the anticipated hazards should be thoroughly examined. Specifications of safety helmets should then be prepared accordingly. The selection procedures should also cover purchasing arrangement and inspection of safety helmets upon receipt.
Implementation of the head protection programme:
Employers have the ultimate responsibility and duty for the execution of the head protection programme which should also cover the provision of information, instruction, training and supervision. To ensure the effective implementation, an effective communicating arrangement should be
established so that all managers, supervisors and workers are fully aware of the potential hazards, precautions to be adopted and their roles to play. Special attention should be paid on the operational supervision to ensure that the safety helmets are used and used properly; and a record keeping
arrangement is available to monitor the performance.
Validation: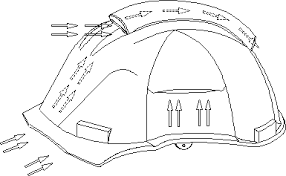
The procedures laid down as well as the responsibilities established throughout the organisation for the use of safety helmets should be periodically reviewed to see how and how good the programme is performing and whether adjustment or improvement is required. Particular attention should be paid to the change of any process which may render safety helmets selected ineffective and may constitute hazards for which additional control measures are required. As far as possible, feedback from workers should be sought during the review. This will certainly improve the effectiveness of the system and the users' acceptance of the safety helmets selected.
Auditing planning:
An auditing plan should be established to ensure long term adequacy of selection decisions and proper use of safety helmets. The auditing process should review new or revised standards requiring protection, injury statistics, workers' acceptance, changes in processes and the availability of alternative control measures.
Service Life:
One common misconception is that hard hats have a predetermined service life - that is not the case. Both the 1986 and 1997 ANSI standards address service life under maintenance and care of the hard hat. All hard hat components should be inspected daily for signs of dents, cracks, penetration and any damage due to impact, rough treatment, or wear. Although it is not considered a "shelf life", some hard hats do have "Useful Service Life Guidelines". These guidelines suggest replacing the suspension every 12 months and the hard hat after 5 years of use. Any hard hat that fails the visual inspection should be removed from service until the problem is corrected.
In addition to everyday wear and tear, ultraviolet (UV) radiation can pose a problem for hats constructed of plastic materials. Damage caused by UV radiation is easy to spot: the hat will lose its glossy finish and eventually take on a chalky appearance. Further degradation could cause the shell to actually start flaking away. Once the effects of UV radiation are detected, the hard hat shell should be immediately replaced.
Safety helmets and their accessories:
Method of protection:
A safety helmet protects against impact from overhead by absorbing energy through -
(a) partial destruction or damage of the shell;
(b) stretching of the harness; and
(c) crushing of the protective padding if any.
The residual force of the impact is spread over the surface of the head thus lessening the chance of injury. To achieve the purpose, stringent performance/test requirements apply to safety helmets.
General Design:
A safety helmet consists of two primary components - shell and harness (Figures A & B).
Figures A Figures B
The shell is a dome-shaped covering for the head and made of hard and durable materials. The outer surface of the shell should be smoothly finished. It may include:
- a brim (a rim surrounding the shell which may include a rain gutter); or/ and
- a peak (a permanent extension of the shell above the eyes).
The harness is the assembly that provides a means of maintaining the helmet in position on the user's head and absorbing kinetic energy within the shell during an impact.
It basically includes:
- a cradle (the assembly of the parts of the harness in contact with the head to maintain the helmet in correct wearing position and with a suspension system to absorb shock in case of an impact);
- a headband (the part of the harness surrounding the head of the user above the eyes); and
- a nape strap (an adjustable strap normally integrated with the headband to fit behind the head).
It may also include:
- a sweatband (an integral or removable strip on the headband that contacts with the user's forehead for removing sweat);
- a chin strap (a strap under the chin to further secure the helmet to the head of the user); or/and
- a protective padding (material contributing to the absorption of kinetic energy during an impact).
Constructional features:
Safety helmets have to fulfil certain mandatory requirements of international/ national standards on the constructional features. These range from the shell profile, the respective clearances between the shell and the harness at various Locations, down to minor details such as the range of adjustable increments of headband and nape strap. Examples are:
- Elliptical shell configuration on horizontal sections above the headband.
- The vertical clearance between the harness and the inside of the shell shall in general be not less than 25 mm and not more than 50 mm.
- The horizontal clearance between the headband and the inside of the shell shall in general be not less than 5 mm and not more than 20 mm.
- Provision shall also be made by ventilation gaps between the shell and the headband.
- The length of the headband or the nape strap shall be adjustable in increments of not more than 5 mm.
Materials used:
The materials for safety helmets should be of durable quality having considered the effect of aging and subjected environments such as sunlight, humidity, temperature and vibration. For those parts coming into contact with the wearer's skin, the materials used should not give rise to irritation.
For the shell, materials commonly used are:
- High density polyethylene (HDPE)
- Acrylonitrile-butadiene-styrene (ABS)
- Poly carbonate (PC)
For the harness, materials commonly used are:
- Nylon
- Vinyl
For the cushioning elements, material commonly used is:
- Sponge foam
Helmet accessories:
There is a wide range of accessories which can be fitted to a safety helmet to make it more suitable for variable working conditions. Examples of accessories are chin strap, face shield, earmuffs, and hand lamp (Figure D to G). Care should be taken to ensure that any addition of helmet accessories and their attachment should be compatible to the helmet. Use of original manufacturer's accessories is recommended. No modification or change of existing helmets should be carried out to fit accessories unless advice from the manufacturer has been sought.
Selection of safety helmets:
Factors in selections:
If there is a need for use of safety helmets, the next step is to ensure the safety helmet provided is appropriate to minimise the effects of the hazards.The helmet chosen should offer the desired protection and comfort and not create any additional safety problems. During the selection process, the following factors are needed to be taken into account:
Potential hazard anticipated:
A part from the primary hazard due to falling objects, additional potential hazards of head injury may also exist in the workplace. It is therefore important to choose a correct type or class of helmets which can also offer protection against those additional hazards anticipated. In construction work, the safety helmet shall offer protection against lateral impact as well, because of the presence of common hazards of striking against protruded objects (e.g. projections from scaffolds, etc.) or being struck by swinging objects(e.g.crane hooks).For electrical work,the safety helmet shall be adequately
electrically insulated. For an extremely cold working environment, the safety helmet shall be so designed that it can still offer the intended protection at such an extra low temperature.
The style of helmet:
- The cap style (Figure H) is generally lighter and the peak will provide shade to the eyes. This style is more suitable for working in restricted or narrow places and for the wearing of accessories such as earmuffs, welding screens, etc.
- The hat style (Figure I) generally provides better protection to the face and neck from the weather, dirt and water, etc.
- Whenever possible, the safety helmet should be selected on the basis that it will not hinder the work to be done. For example, a safety helmet with little or no peak is helpful to have an unrestricted upward vision for a scaffold erector at work.
- The design of the safety helmet selected should be compatible with other necessary accessories or personal protective equipment so that they all remain effective.
The colour of safety helmet:
Safety helmets with lighter colour will provide better heat reflection and good conspicuous. White helmets are therefore suitable for working environments with poor lighting conditions.
In working places where maximum conspicuous is required such as tunnelling work, the colour of safety helmets should be conspicuous against the background or at least part of the exterior surface of the helmet should be retro reflective, or have retro reflective material adhered to it, at all sides.
However, before any application of adhesive tape, advice from manufacturer should be sought to ensure that the adhesive tape will not degrade the shell material.
Appropriate accessories for the work environment: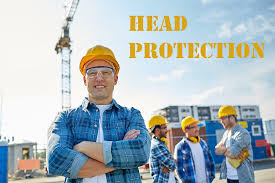
- Safety helmets selected should suit the actual working environment. For example, if the work is to be done at night and the workplace is in poor lighting conditions, the helmet shell should be equipped with head lamp.
- Where the job involves work in windy conditions, repeated bending or constantly looking upwards, chin straps should be provided and used.
Comfort and fitness:
Wearing comfort and fitness of safety helmets should also be considered during selection:
- Safety helmets should be as comfortable as possible. Comfort can be improved by: use of light material for the shell without affecting the design strength; a flexible headband of adequate width to fit the forehead; a sweatband that is easy to clean or replace; and textile cradle straps, etc.
- Fitness is one of the important elements for ensuring the proper functioning of safety helmets in case of an impact. A properly fitting safety helmet should have the right shell size for the wearer and an easily adjustable headband, nape and chin strap.
International/ National standards:
Safety helmets should satisfy certain performance/test requirements, including resistance to penetration, shock absorption, electrical insulation, resistance to flame and various working temperature, etc. Each design should have its own specifications to suit the working environment and the work to be done.
A suitable safety helmet will mean one which is conforming to international/ national standards. Some of commonly used standards are as follows:
- American National Standard - For industrial head protection (ANSI Z89.1)
- Australian/New Zealand Standard - Occupational protective helmets (AS/NZS 1801)
- Canadian Standard - Safety helmets (CSA Z94.1)
- European Standard - Specification for industrial safety helmets (EN 397)
- International Standard - Industrial safety helmets (ISO 3873)
- Japanese Industrial Standard - Industrial safety helmets (JIS T 8131)
- People's Republic of China National Standard - Safety helmets (GB 2811)
- Singapore Standard - Specification for industrial safety helmets(SS 98)
A safety helmet should bear appropriate marking indicating the conformity to certain international/ national standards. For example, every safety helmet complying with the requirements of the European Standard (EN 397) shall carry moulded or impressed marking giving the following information:
- number of this standard;
- name or identification mark of the manufacturer;
- year and quarter of manufacture;
- type of helmet (manufacturer's designation) - this shall be marked on both the shell and the harness;
- size or size range(in centimetres) - this shall be marked on both the shell and the harness.
In addition, a label/sheet shall be attached to/accompany each helmet giving additional information on the usage and safe practices, etc.
International/national standards only set out the minimum requirements of various types/classes of safety helmets. It should be noted that different brands of safety helmets may not be of the same quality even though they all complied with the same standard.
In addition to complying with international/national standards, design features, performance, application and quality matters should also be carefully considered for selecting the most suitable safety helmet.
Specifications of different brands/types of safety helmets available in the markets can be obtained from the personal protective equipment manufacturers. Employers or contractors are advised to seek all relevant information for analysis before making the final decision.
Use of safety helmets:
Provision:
Safety helmets should be provided for the use of workers in the workplace where there is a foreseeable risk of head injury. Records for the receipt of safety helmet should be kept.
Sufficient safety helmets should be available at the workplace for necessary replacement and the use of visitors too.
Manufacture information:
Manufacturer's instructions are normally supplied with each safety helmet indicating the method of fitting and adjustment, care and maintenance, etc. These instructions should be brought to the attention of users. Special attention should be taken to the inspection before use, maintenance procedures, proper storage techniques in accordance with the manufacturer's recommendations and instruction
Training:
Proper training should be provided to each user. Records of training should be kept. The scope of the training should include the following:
- The risks of head injury in workplaces;
- Preventive measures for head injury;
- Why safety helmets are necessary;
- When should it be worn;
- Legal obligations;
- Basic principle on how the safety helmet provides protection;
- Proper methods of wearing;
- Use of accessories and their attachment methods;
- Safe practices (e.g. check before use);
- Care and maintenance; and
- Service life and replacement.
Users should be reminded that the safety helmet is only the last resort and appropriate preventive measures should be taken in order to prevent head injury.
Safe practices:
Safety helmets should be free from defects. The safety helmets if damaged must be handed over to a responsible person for replacement and discarded. The helmets should be marked 'defective'.
- Safety helmets should be checked before use. All parts of the safety helmet must be operational and undamaged, in particular the correct assembly of the shell and harness. In case of any doubt, the manufacturer should be consulted.
- Safety helmets should be adjusted to fit the size of the users' heads for adequate protection.
- Applying paints, solvents or adhesives may weaken the shells without any visual damage. Where names or other markings are to be applied on the safety helmets, advice from the manufacturer should be sought.
- Where accessories are being used, they should be fully compatible to the safety helmet worn. Use of original manufacturer's accessories is recommended.
- Chin straps should be used if a job involves work in windy conditions or needs frequent bending or looking upward /downward.
- Safety helmets should be worn in the correct way - In summer time, some workers wear straw hats between safety helmets and their heads in order to reduce the exposure of sunlight. Such practice however significantly reduces the protection of safety helmets and should be prohibited.
- Safety helmets should not be transferred by throwing as the helmet may accidentally fall on the floor receiving a severe impact that weakening its strength as a result.
- Safety helmets should not be used for other purpose than that they are designed, such as seats, receptacles and steps, etc.
- After use, the users should place their safety helmets in a safe place that may be provided by the employers or contractors.
- The shell and harness should be periodically cleaned to remove dirt, dust, grease or mud, etc. The sweatband should also be cleaned regularly or replaced.
Care and maintenance of safety helmets:
Proper care and maintenance of safety helmets are very important in providing the intended protection to workers over their intended service life. Procedures for care and maintenance should be adhered to in accordance with manufacturer's instructions. Responsibilities for care and maintenance of safety helmets should be clearly established within the workplace/ organisation.
Care and maintenance of safety helmets include storage, cleaning, inspection and replacement.
Storage: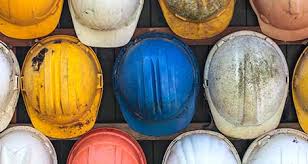
Safety helmets should be properly stored in a safe place with no direct sunlight, no excessive heat and a non-humid condition. Long-term exposure of extreme environmental conditions can reduce the strength and efficiency of the helmets. For example, the safety helmet should not be kept on the rear-window shelf of a vehicle. Sunlight and high temperature may cause degradation and the helmet might also become a hazardous missile in an emergency stop.
Adequate storage rooms, containers or pegs should be provided for storing safety helmets to protect against contamination, loss or damage. These storage areas should preferably be located at the entrance of the workplace so that every person can put on his helmet once he enters the site. Users have the responsibility to place their safety helmets in the safe places when not in use.
Cleaning:
Cleaning is the process for removal of soiling or surface contamination suchas dirt, dust, grease, mud or body oils, etc. Regular cleaning should be carried out in accordance with the manufacturer's
instructions. General cleaning method using soapy water and a soft cloth is acceptable. Use of cleaning solvents should be avoided as it may deteriorate the plastic of the shell without any visual damage. The sweatband should also be cleaned regularly or replaced where necessary.
Inspection:
Before issuing safety helmets to workers for use, each helmet should be inspected to ensure it is in good condition.
Daily inspection of safety helmets should be conducted to ensure that they are in a serviceable state without any defect. All components, shells, harnesses and accessories should be checked for signs of dents, cracks, penetration, brittleness or deterioration which may reduce the strength and efficiency of safety helmets. The harnesses should also be checked for proper fitness to the shells.
Periodic inspection, such as quarterly inspection, is required to determine the need for disposal and replacement.
Lifetime and replacement:
Safety helmets should have a limited lifetime because of material degradation that can take place due to sunlight, heat or material self-degradation. Suppliers or manufacturers should be consulted for acquiring the lifetime of safety helmets.
Service life of safety helmets is a function of several factors including materials used, quality control, usage conditions, care and maintenance. It is very difficult to accurately determine as helmets are used in various conditions, ranging from the very harsh to the very light.
Under normal services, most helmet shells can provide adequate protection for about 2 to 3 years. Plastic components of harnesses may deteriorate more rapidly in service and so harnesses should be replaced at intervals not longer than 2 years. It should be noted that signs of damage or deterioration may be observed in a much shorter service life. Should such be a case, the safety helmet should be immediately withdrawn from service and discarded.
Safety helmets cannot be repaired. It is therefore important that replacement of the safety helmet is required if it has been subjected to a severe impact regardless of the service life and whether there is any physical damage to the helmet or not, since the design strength and effectiveness have been
greatly reduced.
Click the below link to download head protection documents
Head protection -Tool Box Talk
Head protection - Power point presentation
Head protection - Safety check sheet
Safety helmet testing video
Head protection in work place