Sling - Wire Rope Sling :
Wire rope is often used in slings because of its strength, durability, abrasion resistance and ability to conform to the shape of the loads on which it is used. In addition, wire rope slings are able to lift hot materials.
Wire rope used in slings can be made of ropes with either Independent Wire Rope Core (IWRC) or a fiber-core. It should be noted that a sling manufactured with a fiber-core is usually more flexible but is less resistant to environmental damage. Conversely, a core that is made of a wire rope strand tends to have greater strength and is more resistant to heat damage.
Wire rope may be manufactured using different rope lays. The lay of a wire rope describes the direction the wires and strands are twisted during the construction of the rope. Most wire rope is right lay, regular lay. This type of rope has the widest range of applications. Wire rope slings may be made of other wire rope lays at the recommendation of the sling manufacturer or a qualified person.
Wire rope slings are made from various grades of wire rope, but the most common grades in use are Extra Improved Plow Steel (EIPS) and Extra Extra Improved Plow Steel (EEIPS). These wire ropes are manufactured and tested in accordance with ASTM guidelines. If other grades of wire rope are used, use them in accordance with the manufacturer's recommendations and guidance.
When selecting a wire rope sling to give the best service, consider four characteristics: strength, ability to bend without distortion, ability to withstand abrasive wear, and ability to withstand abuse.
Identification:
New slings are marked by the manufacture to show:
- The rated load for the types of hitches, and the angle upon which they are based,
- The diameter or size, and
- The name or trademark of the manufacturer.
Rated loads:
Rated loads (capacities) for single-leg vertical, choker, basket hitches, and two-, three-, and four-leg bridle slings for specific grades of wire rope slings are as shown in Tables 7 through 15.
For angles not shown, use the next lower angle or a qualified person to calculate the rated load. Rated loads are based on:
- Material strength,
- Design factor,
- Type of hitch,
- Angle of loading,
- Diameter of curvature over which the sling is used (D/d) (see Fig. 4), and
- Fabrication efficiency.
Fig-4d/D
The symbols below represent load or support surfaces in contact with the rope sling. The contact surface diameter divided by the rope diameter is designated D/d ratio as described in Fig. 6. Tables 18, 19, and 20 are based on the D/d ratios indicated below.
Do not use horizontal angles less than 30 degree except as recommended by the sling manufacturer or a qualified person.
Configurations:
- Ensure that slings made of rope with 6x19 and 6x37 classifications and cable slings have a minimum clear length of rope 10 times the component rope diameter between splices, sleeves, or end fittings unless approved by a qualified person,
- Ensure that braided slings have a minimum clear length of rope 40 times the component rope diameter between the loops or end fittings unless approved by a qualified person,
- Ensure that grommets and endless slings have a minimum circumferential length of 96 times the body diameter of the grommet or endless sling unless approved by a qualified person, and
- You may use other configurations if specific data is supplied by the manufacturer or a qualified person.
Rated loads for a sling in a choker hitch are the values shown in Table 7, 9, 11, 13, 14, or 15, provided that the angle of the choke is 120 degrees or more (Fig. 2). Use the values in Fig. 2 or those from the sling manufacturer or a qualified person for angles of choke less than 120 degrees.
For other materials and for configurations not shown, use the rated loads provided by the sling manufacturer or a qualified person.
Table 7
Rated Load for Single- and Two-Leg Slings 6×19 or 6×36 Classification
Extra Improved Plow Steel (EIPS) Grade Fiber Core (FC) Wire Rope
Based on Design Factor = 5 and Rated Loads Expressed in Tons (2,000 lb)
GENERAL NOTES:
HT = hand-tucked splice.
MS = mechanical splice.
S = swagged or poured socket.
Rated loads based on minimum D/d ratio of 25/1.
(e) Rated load based on pin diameter no larger than natural eye width or less than the nominal sling diameter.
(f) For choker hitch, the angle of choke is 120 deg or greater.
Table 9
Rated Load for Single-and Two-Leg Slings 6×19 or 6×36 Classification
Extra Improved Plow Steel (EIPS) Grade Independent Wire Rope Core (IWRC) Wire Rope
Based on Design Factor = 5 and Rated Loads Expressed in Tons (2,000 lb)
GENERAL NOTES:
HT = hand-tucked splice.
MS = mechanical splice.
S = swagged or poured socket.
Rated loads based on minimum D/d ratio of 25/1.
(e) Rated load based on pin diameter no larger than natural eye width or less than the nominal sling diameter.
(f) For choker hitch, the angle of choke is 120 deg or greater.
Table 11
Rated Load for Single- and Two-Leg Slings 6×19 or 6×36 Classification
Extra Extra Improved Plow Steel (EEIPS) Grade Independent Wire Rope Core (IWRC) Wire Rope
Based on Design Factor = 5 and Rated Loads Expressed in Tons (2,000 lb)
GENERAL NOTES:
HT = hand-tucked splice.
MS = mechanical splice.
S = swagged or poured socket.
Rated loads based on minimum D/d ratio of 25/1.
(e) Rated load based on pin diameter no larger than natural eye width or less than the nominal sling diameter.
(f) For choker hitch, the angle of choke is 120 deg or greater.
Fig. 2 Angle of Choke
Table 13
Rated Load for Cable-Laid Wire Rope Single- and Two-Leg Slings
Mechanical Splice Only
Based on Design Factor = 5 and Rated Loads Expressed in Tons (2,000 lb)
GENERAL NOTES:
(a) 7X7X7 = galvanized specialty cable.
(b) 7X7X19 = galvanized specialty cable.
(c) Rated loads based on minimum D/d ratio of 10/1.
(d) Rated loads based on pin diameter no larger than natural eye width or less than the nominal sling diameter.
(e) For choker hitch, the angle of choke is 120 deg or greater.
End attachments:
Perform welding of handles or other accessories to end attachments, except covers to thimbles, before assembly of the sling. Ensure that welded end attachments are proof tested by the manufacturer or a qualified person. Retain the certificates of proof test and make them available for examination. Use components such as sleeves and sockets in accordance with the manufacturer's recommendation.
Wire rope clips and hooks:
- Do not use knots to fabricate your own slings,
- Do not use wire rope clips to fabricate wire rope slings, except where the application precludes the use of prefabricated slings and where the sling is designed for the specific application by a qualified person,
- Install wire rope clips according to the recommendations of the manufacturer or a qualified person,
- Do not use slings made with wire rope clips in a choker hitch,
- Use only wire rope clips made from drop-forged steel of the single-saddle (U-bolt) or double-saddle type clip,
- Do not use malleable cast iron clips to fabricate slings,
- Refer to the clip manufacturer for spacing, number of clips, and torque values,
- Attach U-bolts to wire rope clips with the U-bolt over the dead end of the rope and the live rope resting in the clip saddle,
- Tighten clips evenly to the recommended torque before and after the initial load is applied,
- Regularly inspect clips to ensure that the recommended torque remains, and
- Inspect clips periodically for wear, abuse, or damage.
Table 14
Rated Load for Six-Part Braided Single- and Two-leg Slings 6x19 or 6x36
Classification Extra Improved Plow Steel (EIPS) Independent Wire Rope Core (IWRC) Wire Rope
Based on Design Factor = 5 and Rated Loads Expressed in Tons (2,000 lb)
(or)
Table 15
Rated Load for Eight-Part Braided Single- and Two-leg Slings 6x19 or 6x36
Classification Extra Improved Plow Steel (EIPS) Independent Wire Rope Core (IWRC) Wire Rope
Based on Design Factor = 5 and Rated Loads Expressed in Tons (2,000 lb)
Inspections:
Designate a qualified person1 to inspect slings and all fastenings and attachments each day before use for damage or defects.
The qualified person also performs additional periodic inspections where service conditions warrant, as determined on the basis of:
- Frequency of sling use,
- Severity of service conditions,
- Nature of the lifts being made, and
- Experience gained during the service life of slings used in similar circumstances.
Make periodic inspections of wire rope slings at intervals no greater than 12 months. A good guide to follow includes:
- Yearly for normal service use,
- Monthly to quarterly for severe service use, and
- As recommended by a qualified person for special and infrequent service use.
Although OSHA's sling standard does not require you to make and maintain records of inspections, the ASME standard contains provisions on inspection records.
Make a thorough inspection of slings and attachments. Items to look for include:
- Broken wires,
- Severe localized abrasion or scraping,
- Kinking, crushing, bird caging, or any other damage to the rope structure,
- Evidence of heat damage,
- Crushed, deformed, or worn end attachments,
- Severe corrosion of the rope, end attachments or fittings,
- Missing or illegible sling identifications, and
- Other conditions that cause doubt as to continual safe use of the sling.
Where any such defect or deterioration is present, remove the sling or attachment from service immediately.
Repairing/Reconditioning:
Do not use worn or damaged slings or attachments. Discard or repair them.
Use damaged slings only after they are repaired, reconditioned, and proof tested by the sling manufacturer or a qualified person using the following criteria:
- Do not repair wire rope used in the sling,
- Restrict all repairs to end attachments and fittings, and
- Mark repaired slings to identify who made the repairs.
Modifications or alterations to end attachments or fittings are considered a repair.
Operating practices:
Ensure that wire rope slings have suitable characteristics for the type of load, hitch, and environment in which they will be used and that they are not used with loads in excess of the rated load capacities described in the appropriate tables. When D/d ratios (Fig. 4) are smaller than those listed in the tables, consult the sling manufacturer. Follow other safe operating practices, including:
Sling Selection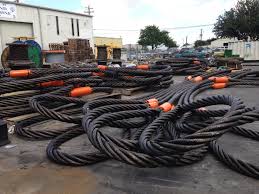
- For multiple-leg slings used with non symmetrical loads, ensure that an analysis by a qualified person is performed to prevent overloading of any leg,
- Ensure that multiple-leg slings are selected according to Tables 7 through 15 when used at the specific angles given in the tables. Ensure that operations at other angles are limited to the rated load of the next lower angle given in the tables or calculated by a qualified person,
- When using a multiple-leg sling, ensure that the rating shown for the single-leg sling is not exceeded in any leg of the multiple-leg sling,
- When D/d ratios (see Fig. 6) smaller than those cited in the tables are necessary, ensure that the rated load of the sling is decreased. Consult the sling manufacturer for specific data or refer to the WRTB (Wire Rope Technical Board) Wire Rope Sling Users Manual, and
- Do not use a fitting unless it is of the proper shape and size to ensure that it seats properly in the hook or lifting device.
Cautions to Personnel
- Ensure that all portions of the human body are kept away from the areas between the sling and the load and between the sling and the crane or hoist hook,
- Ensure that personnel never stand in line with or next to the legs of a sling that is under tension,
- Ensure that personnel do not stand or pass under a suspended load,
- Ensure that personnel do not ride the sling or the load, unless the load is specifically designed and tested for carrying personnel, and
- Do not inspect a sling by passing bare hands over the wire rope body. Broken wires, if present, may puncture the hands.
Effects of Environment:
- Store slings in an area where they will not be subjected to mechanical damage, corrosive action, moisture, extreme temperatures, or to kinking,
- When slings are exposed to extreme temperatures, follow the guidance provided by the sling manufacturer or a qualified person,
- Do not subject fiber-core wire rope slings to degreasing or to a solvent because of possible damage to the core, and
- Follow the manufacturer's lubrication requirements.
Sling made with a triangle fitting on one end and a slotted triangle choker fitting on the other end. It can be used in a vertical, basket, or choker hitch.
Rigging Practices:
- Ensure that slings are hitched in a manner providing control of the load,
- Ensure that sharp edges in contact with slings are padded with material of sufficient strength to protect the sling,
- Ensure that slings are shortened or adjusted only by methods approved by the sling manufacturer or a qualified person,
- Ensure that, during lifting with or without a load, personnel are alert for possible snagging,
- Ensure that, in a basket hitch, the load is balanced to prevent slippage,
- When using a basket hitch, ensure that the legs of the sling contain or support the load from the sides, above the center of gravity, so that the load remains under control,
- Ensure that, in a choker hitch, the choke point is only on the sling body, never on a fitting,
- Ensure that, in a choker hitch, an angle of choke less than 120 degrees is not used without reducing the rated load,
- Ensure that slings are not constricted, bunched, or pinched by the load, hook, or any fitting,
- Ensure that the load applied to the hook is centered in the base (bowl) of the hook to prevent point loading on the hook, unless the hook is designed for point loading,
- Ensure that an object in the eye of a sling is not wider than one half the length of the eye,
- Ensure that the sling is allowed to rotate when hand-tucked slings are used in a single leg vertical lift application. Minimize sling rotation,
- Do not shorten or lengthen a sling by knotting or twisting,
- Do not rest loads on the sling,
- Do not pull a sling from under a load when the load is resting on the sling,
- Do not drag slings on the floor or over abrasive surfaces,
- Do not use slings made with wire rope clips as a choker hitch, and
- Do not allow shock loading.
Proof testing:
Before initial use, ensure that all new swaged-socket, poured-socket, turnback-eye, mechanical joint grommets, and endless wire rope slings are proof tested by the sling manufacturer or a qualified person.
Other new wire rope slings need not be proof tested, although the employer may require proof testing in purchasing specifications.
Ensure that all welded end attachments are tested by the manufacturer or equivalent entity at twice their rated capacity before initial use.
Environmental Effects:
Permanently remove from service fiber-core wire rope slings of any grade if they are exposed to temperatures in excess of 180 degrees F (82 degrees C).
Follow the recommendations of the sling manufacturer when you use metallic-core wire rope slings of any grade at temperatures above 400 degrees F (204 degrees C) or below minus 40 degrees F (minus 40 degrees C).
Chemically active environments can affect the strength of wire rope slings. Consult the manufacturer before using a sling in such environments.
Click the below link to download wire rope safety check sheet
Sling - Steel Chain, Wire Rope, and Metal Mesh safety check sheet