Organic Peroxide:
Introduction:
An organic peroxide is any organic (carbon-containing) compound having two oxygen atoms joined together (-O-O-). This chemical group is called a "peroxy" group. Organic peroxides can be severe fire and explosion hazards. This question-and-answer document summarizes these and other hazards; another document provides information on how to work safely with organic peroxides.
The plastics and rubber industries are the heaviest users of organic peroxides. Organic peroxides and mixtures containing an organic peroxide are used as accelerators, activators, catalysts, cross-linking agents, curing agents, hardeners, initiators and promoters. Organic peroxides and mixtures containing an organic peroxide are often referred to by these terms. However, using terms like accelerator, activator, etc. to mean "organic peroxide" can be misleading since they can also refer to materials that do not contain organic peroxides. This can cause confusion and a serious accident could result if these substances were mixed with organic peroxides.
Organic peroxides are available as solids (usually fine powders), liquids or pastes. Some materials, such as water, odourless mineral spirits, and some phthalate esters do not react with organic peroxides and are often used to dilute them. The diluted mixtures or formulations are less likely to explode when exposed to heat or physical shock than the undiluted organic peroxide. Dilution makes the unstable peroxides safer to produce, handle, and use. We use the term "organic peroxide" to refer to both undiluted and diluted organic peroxides, unless otherwise specified. Check the supplier labels on chemical product containers.
The Canadian WHMIS (Workplace Hazardous Materials Information System) 1988 classifies organic peroxides as oxidizing materials. WHMIS 1988 also classifies many other materials that are not organic peroxides as oxidizing materials. Other hazard symbols may also be present, depending on the particular material.
It is wise to treat any unknown material as very hazardous until it is positively identified.
How are organic peroxides hazardous:
The main hazard related to organic peroxides are their fire and explosion hazards. Organic peroxides may also be toxic or corrosive. Depending on the material, route of exposure (inhalation, eye or skin contact, or swallowing) and dose or amount of exposure, they could harm the body. Corrosive organic peroxides can also attack and destroy metals.
It is the double oxygen of the "peroxy" group that makes organic peroxides both useful and hazardous. The peroxy group is chemically unstable. It can easily decompose, giving off heat at a rate that increases as the temperature rises. Many organic peroxides give off flammable vapours when they decompose. These vapours can easily catch fire.
Most undiluted organic peroxides can catch fire easily and burn very rapidly and intensely. This is because they combine both fuel (carbon) and oxygen in the same compound. Some organic peroxides are dangerously reactive. They can decompose very rapidly or explosively if they are exposed to only slight heat, friction, mechanical shock or contamination with incompatible materials.
Organic peroxides can also be strong oxidizing agents. Combustible materials contaminated with most organic peroxides can catch fire very easily and burn very intensely (i.e., deflagrate). This means that the burn rate is very fast: it can vary from 1 m/sec to hundreds of metres per second. Also the combustion rate increases as the pressure increases and the combustion (or reaction) zone can travel through air or a gaseous medium faster than the speed of sound. However, the speed of combustion in a solid medium does not exceed the speed of sound.
This is one characteristic that distinguishes deflagration from detonation. We mention these two terms because they are used in classifying organic peroxide formulations (see next question). Deflagrations and detonations are similar chemical reactions except that in detonations the burn rate in a solid medium is faster than the speed of sound. This supersonic speed results in a shock wave being produced. They can transmit the shock wave at speeds of about 2,000 to 9,000 m/sec and is not dependent on the surrounding pressure. This is another difference between detonation and deflagration: deflagration rates increase as the pressure becomes greater.
Explosive decomposition is a rapid chemical reaction resulting in almost instantaneous release of energy. This term includes both deflagration and detonation.
Organic peroxides may also have a self accelerating decomposition temperature (SADT). SADT represents the lowest temperature in which that particular organic peroxide formulation in its commercial packaging will undergo self-accelerating decomposition (begin the chemical process that leads to explosion). The SADT value will vary with each organic peroxide formulation and the size and shape of its packaging. Storage requirements will generally be 10 to 20 degrees below the SADT.
Is it important to have an MSDS for organic peroxides: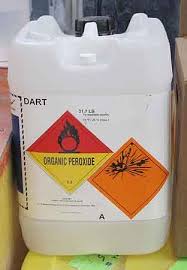
The MSDSs and the container labels should explain all of the hazards of the organic peroxides with which you work. For example, the MSDS should describe the conditions that cause an organic peroxide formulation to undergo dangerous chemical reactions and cause explosions. They also should state if there are any special storage requirements. Some should be stored in a refrigerator to reduce the possibility of fire and the refrigerator should meet the electrical code requirements for the products being stored (e.g., should be "explosion-proof"). The MSDS should say if there is a minimum temperature under which the product should not be stored. If the temperature is too low, crystals of the peroxide may form. These crystals could be an explosion hazard since they can be very sensitive to shock.
Example of an organic peroxide:
An example of an organic peroxide is methyl ethyl ketone peroxide (also known as 2-butanone peroxide, ethyl methyl ketone peroxide, or MEKP). It is used as a polymerization catalyst in the manufacture of polyester and acrylic resins and as a hardening agent for fiberglass reinforced plastics. It is a colorless liquid with a characteristic odour. It is considered a combustible liquid and vapour. There is an extreme risk of an explosion from exposure to shock, friction, flame, or other sources of ignition. It is dangerously reactive and may decompose violently. Contact with water or moist air liberates irritating gases. Contents may develop pressure if exposed to water. It is also very toxic. It may be fatal if inhaled, absorbed through the skin or swallowed and it is corrosive to the eyes, skin and respiratory tract. It may cause lung injury although the effects may be delayed.
Organic peroxides form spontaneously:
- Yes, some chemicals can form explosive peroxides when they are stored (e.g., isopropyl ether, vinylidene chloride). Exposure to light and heat can increase the rate of peroxide formation. Others form peroxides that become hazardous when concentrated (e.g., by distillation). Some examples include ethyl ether, tetrahydrofuran (THF), p-dioxane, some secondary alcohols like 2-propanol and 2-butanol, and some unsaturated hydrocarbons like propyne (an acetylene compound), cyclohexene, and tetra-and deca-hydronaphthalenes.
- Another kind of peroxide-forming compound are unsaturated monomers that, in the presence of a peroxide, can polymerize exothermically (i.e., produces heat when it reacts). For example, uninhibited styrene can form a peroxide that can cause the styrene to polymerize. It can occur explosively under certain conditions. Other examples of some unsaturated monomeric compounds are acrylic acid, acrylonitrile, butadiene, methyl methacrylate, and vinyl chloride.
- To generalize, the kinds of chemicals that can form peroxides include aldehydes, ethers, and numerous unsaturated hydrocarbon compounds (i.e. hydrocarbon compounds having double or triple bonds). Examples in this group include allyl compounds, haloalkenes, dienes, monomeric vinyl compounds, vinylacetylenes, unsaturated cyclic hydrocarbons like tetrahydronaphthalene or dicyclopentadiene.
- This is not a comprehensive list. The intention of mentioning these examples is to point out the importance of learning about the hazards of the chemicals you handle by reading the MSDSs and any relevant safety bulletins that the chemical producers provide. They should recommend how frequently they should be tested for the presence of peroxides (e.g., once every 3 months for diisopropyl ether or vinylidene chloride; once every 12 months for ethyl ether). Follow their directions regarding the safe disposal or repurifications procedures (if recommended).
- So if, for example, you see crystals inside a bottle of a "pure" ether, suspect the presence of an ether peroxide. Do not handle the container. Do call your emergency response group. They should contact the local bomb squad after assessing the situation. Ether peroxides, like other peroxides, are very sensitive to shock and could explode if handled improperly - just like a bomb.
Classification system used for organic peroxides by the US National Fire Protection Association:
The U.S. National Fire Protection Association (NFPA) has developed a hazard classification system for typical organic peroxide formulations. The NFPA classification system describes the fire and explosion hazards of these formulations in their normal shipping and storage containers that have been approved by the Transport Canada or the U.S. Department of Transport (DOT).
If a formulation is transferred to a different container, the given hazard classification may no longer apply. See the NFPA 432 "Code for the Storage of Organic Peroxide Formulations" (2002) for details. In general:
- Class I formulations are capable of deflagration but not detonation.
- Class II formulations burn very rapidly and are a severe reactivity hazard.
- Class III formulations burn rapidly and have a moderate reactivity hazard.
- Class IV formulations burn in the same manner as ordinary combustibles and have a minimal reactivity hazard.
- Class V formulations burn with less intensity than ordinary combustibles or they do not support combustion and present no reactivity hazard.
Storing organic peroxide: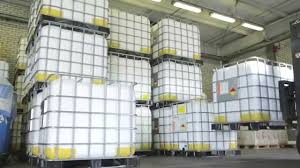
- Before storing, inspect all incoming containers to ensure that they are undamaged and properly labelled. Do not accept delivery of defective containers.
- Store organic peroxides in the containers that the chemical supplier recommends. Normally, these are the same containers in which the material was shipped. Repackaging can be very dangerous, especially when using contaminated or incompatible containers.
- Make sure containers are suitably labelled. For organic peroxides requiring temperature control, the recommended storage temperature range should be plainly marked on the container. It is also a good practice to mark the date that the container was received and the date it was first opened. Store according to self accelerating decomposition requirements (SADT) as well.
- Protect containers against impact or other physical damage, when storing, transferring or using them. Do not use combustible pallets, such as wood, for storing organic peroxide containers.
- Normally, keep containers tightly closed to avoid contamination in storage except when the supplier's instructions state otherwise.
- Storing open or partly open containers of peroxides diluted with solvents, including water, can lead to evaporation of the solvent. This can expose the more hazardous dry peroxide.
- Some liquid organic peroxides, however, such as methyl ethyl ketone peroxide, gradually decompose giving off gas. These peroxides are shipped in containers with specially vented caps. Use no other type of cap for containers of these organic peroxides. The vent caps relieve the normal buildup of gas pressure that could shatter an unvented container. Check vent caps regularly to ensure that they are working properly. Keep vented containers in an upright position. NEVER stack vented containers on top of each other.
Aware of in the organic peroxide storage area:
Store organic peroxides separately, away from processing and handling areas. Keep them away from incompatible materials such as strong acids and bases, other oxidizing materials, flammable or combustible liquids and materials that can be oxidized (often called reducing materials or agents). Separate storage can reduce personal injury and damage caused in case of fires, spills or leaks.
Check the reactivity data and storage requirements sections of the MSDS for details about what materials are incompatible with a specific organic peroxide.
Construct walls, floors, shelving and fittings in storage areas from noncombustible materials that are compatible with the organic peroxides.
Ensure that floors are resistant to penetration by the organic peroxides in storage. Floors should have no cracks in which chemicals could lodge if spilled.
Since liquid organic peroxides flow easily, provide dikes around large liquid storage areas and sills or ramps at door openings. Store smaller amounts in trays made from compatible materials to contain spills or leaks.
Store containers at a convenient height for handling, below eye level if possible, to reduce the risk of dropping them. Avoid overcrowding in storage areas. Do not store containers in out-of-the-way locations where they could be forgotten.
Store containers away from doors. Although it is convenient to place frequently used materials next to the door, they could cut off the escape route if an emergency occurs.
Store organic peroxides in areas which are:
- Well ventilated.
- Out of direct sunlight and away from steam pipes, boilers or other heat sources.
- At temperature as recommended by manufacturer/supplier. Always keep the storage area within the recommended temperature range.
- Supplied with adequate firefighting equipment, including sprinklers.
- Supplied with suitable spill clean-up equipment and materials.
- Free of ignition sources such as open flames, hot surfaces, burning tobacco and spark-producing tools and devices.
- Accessible at all times.
- Labelled with suitable warning signs.
At all times:
- Allow only trained, authorized people into storage areas.
- Keep the amount of organic peroxides in storage as small as possible.
- Inspect storage areas regularly for any deficiencies including damaged or leaking containers and poor housekeeping.
- Correct all deficiencies as soon as possible.
Dispensing or transferring organic peroxides:
- Open and dispense containers of organic peroxides in a special room or area outside the storage area. Do not allow any ignition sources in the vicinity. Take care that the organic peroxides do not contact combustible or other incompatible materials when they are dispensed.
- Use containers and dispensing equipment such as drum pumps, scoops or spatulas that the chemical supplier recommends. These items must be made from non-sparking materials compatible with the peroxides used. Keep them very clean to avoid contamination.
- When transferring organic peroxides from one container to another, avoid spilling or contaminating your skin or clothing. Spills from open, unstable or breakable containers during material transfer have caused serious accidents.
- Never transfer liquids by pressurizing their usual shipping containers with air or inert gas. The pressure may damage ordinary drums and barrels. Moreover, if air is used, it may create a flammable atmosphere inside the container.
- Glass containers with screw-cap lids or glass stoppers may not be acceptable for some organic peroxides, especially those sensitive to friction and grinding. Never transfer materials stored in a vented container into a tightly sealed, non-vented container. The buildup of gas pressure could rupture it. Dispense from only one container at a time. Finish all the dispensing of one material before starting to dispense another. Dispense the smallest amount possible, preferably only enough for immediate use. Keep containers closed after dispensing to reduce the risk of contaminating their contents.
- Never return unused material, even if it does not seem to be contaminated, to the original container.
- If a water-based formulation freezes, do not chip or grind it to break up lumps of material, or heat it to thaw it out. Follow the chemical supplier's advice.
- Avoid dropping, sliding or skidding heavy metal containers such as drums or barrels of friction- or shock-sensitive material.
Handling organic peroxides:
Make sure that all areas where organic peroxides are used are clean and free of combustible and other incompatible materials and any ignition sources. Temperatures in peroxide use areas should be controlled so as to not become high enough to cause rapid decomposition.
Processing Equipment: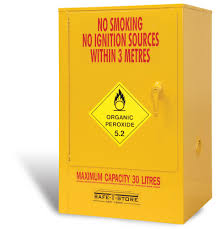
Ensure that processing equipment is clean, properly designed and made from materials compatible with the organic peroxide being used. Find out from the chemical supplier what materials are suitable for the specific peroxide. Copper, brass or lead equipment is dangerous in contact with some organic peroxides at higher temperatures. Some steels and aluminum alloys, zinc and galvanized metal can also cause rapid decomposition of certain organic peroxides.
Diluting Organic Peroxides
Some jobs require diluting organic peroxides prior to use. Do this strictly according to the chemical supplier's advice. Using the wrong solvent or a contaminated solvent could cause an explosion. For example, methyl ethyl ketone peroxide and cyclohexanone peroxide may explode if they are mixed with acetone, a common solvent. Using reclaimed solvents of uncertain composition can also be hazardous. They may contain dangerous concentrations of contaminants that are incompatible with the organic peroxide.
Hazardous Operations:
Some operations involving organic peroxides can be especially hazardous. Accidents have occurred during distillation, extraction or crystallization, because these processes concentrated the organic peroxides. Filtering friction- or shock-sensitive chemicals with materials and devices that produce heat, such as sintered glass filters, can be hazardous.
Before using a new material in an operation, find out as much as possible about the potential hazards of the particular peroxide and operation.
Using Organic Peroxides with Resins:
Organic peroxides are often used as catalysts to activate resins in plastics production. Never mix organic peroxides directly with any accelerators or promoters. A violent explosion may result. Thoroughly mix the accelerator or promoter in the resin mixture before adding the organic peroxide.
It is dangerous to dissolve peroxides in very small amounts of monomer (such as styrene) before adding them to the resin mixture. These "small quantity" mixtures can undergo rapid polymerization giving off a lot of heat. This may result in a fire.
Regular workplace inspections can help to spot situations in which organic peroxides are stored, handled or used in potentially hazardous ways.
Handle emergencies: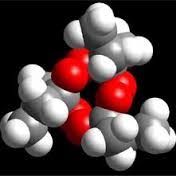
Act fast in emergencies like chemical fires, spills and leaks.
- Evacuate the area at once if you are not trained to handle the problem or if it is clearly beyond your control.
- Alert other people in the area to the emergency.
- Call the fire department immediately.
- Report the problem to the people responsible for handling emergencies where you work.
- Obtain first aid if you have been exposed to harmful chemicals and remove all contaminated clothes.
Check that emergency eyewash stations and safety showers are available wherever accidental exposure to organic peroxides that can damage skin or eyes might occur.
Only specially trained and properly equipped people should handle emergencies. Nobody else should go near the area until it is declared safe.
Planning, training and practicing for emergencies help people to know what they must do. Prepare a written emergency plan. Update it whenever conditions in the workplace change.
The MSDSs for the materials used are a starting point for drawing up an emergency plan. MSDSs have specific sections on spill clean-up procedures, first aid instructions, and fire and explosion hazards including suitable fire extinguishing equipment and methods. If the directions in each MSDS section are unclear or seem incomplete, contact the material's supplier for help.
It is very important to know the best ways to fight fires involving organic peroxides. The "built-in" supply of oxidizing gas in organic peroxides makes extinguishing methods based on smothering ineffective (for example, foam or carbon dioxide). Often, cooling with large amounts of water is the only suitable method.
Basic safe practices concerning organic peroxides:
Following these basic safe practices will help protect you from the hazards of organic peroxides:
- Read the Material Safety Data Sheets (MSDSs) for all of the materials used in your work.
- Know all of the hazards (fire/explosion, health, corrosive, chemical reactivity) of the materials used in your work.
- Know which of the materials you work with are organic peroxides.
- Always follow safe work practices for temperature, avoiding contamination, storage, and quantity (of use).
- Store organic peroxides in suitable, labelled containers (usually their shipping containers).
- Follow the chemical supplier's advice about maximum and minimum storage and use temperatures.
- Know the SADT "danger temperature" and what to do if the organic peroxide is reaching this temperature.
- Inspect containers for damage or leaks before handling them.
- Store, handle and use organic peroxides in well-ventilated areas and away from incompatible materials.
- Eliminate ignition sources (sparks, smoking, flames, hot surfaces) when working with organic peroxides.
- Handle containers safely to avoid damaging them.
- Keep containers closed when not in use.
- Keep only the smallest amounts possible (not more than one day's supply) in the work area.
- Dispense organic peroxides carefully, using compatible equipment, into acceptable containers.
- Do not grind or subject organic peroxides to any type of friction or impact.
- Be careful when performing operations such as distillations or separations that concentrate organic peroxides.
- Never return unused or contaminated organic peroxides to their original containers.
- Return unopened containers to the proper storage area and opened containers to a dispensing or premixing area at the end of the day.
- Practice good housekeeping, personal cleanliness and equipment maintenance.
- Handle and dispose of organic peroxide wastes safely.
- Wear the proper personal protective equipment for each of the jobs you do.
- Know how to handle emergencies (fires, spills, personal injury) involving the organic peroxides you work with. Have trained personnel and planned emergency procedures specific to organic peroxides.
- Follow the health and safety rules that apply to your job.
Click the below link to download the Organic Peroxide guidelines
Storage and Handling of organic peroxide guidelines