Hot work :
Welding and Hot Work, such as brazing or grinding present a significant opportunity for fire and injury. All precautions of this program must be applied prior to commencing any welding or hot work by company employees or contractors. Hot work presents an increased risk of fire and explosion hazards because it is most often performed in confined and enclosed spaces.
Hot Work Permits: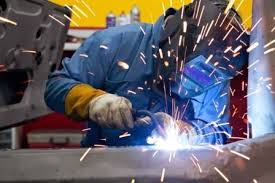
Before hot work operations begin in a non-designated location, a completed hot work permit is required.
The following conditions must be confirmed before permitting the hot work to commence:
- Equipment to be used (e.g. welding equipment, shields, personal protective equipment, fire extinguishers) must be in satisfactory operating condition and in good repair.
- The floor must be swept clean for a radius of 35 ft if combustible materials, such as paper or wood shavings are on the floor, Combustible floors (except wood on concrete) must be kept wet or be covered with damp sand ( note: where floors have been wet down, personnel operating arc welding or cutting equipment shall be protected from possible shock)., or be protected by noncombustible or fire-retardant shields.
- All combustible materials must be moved at least 35 ft away from the hot work operation. If relocation is impractical, combustibles must be protected with fire-retardant covers, shields, or curtains.
- Edges of covers at the floor must be tight to prevent sparks from going under them, including where several covers overlap when protecting a large pile.
- OSHA has very specific regulations covering welding, brazing and cutting operations.
- Ventilation requirements depend on the metals and compounds used. Welding & cutting operations, conducted outside authorized hot work areas, includes extensive procedures for fire prevention.
Welding Hazards:
- burns & fire
- impact
- penetration
- dust, smoke & fumes
- heat
- light radiation
- asphyxiation
Types of Welding & Cutting:
Arc Welding is the process of using an electric current between a metal electrode and base metal. The generated heat melts the metal of the electrode and base metal which combine and then solidify in the weld joint.
The gas Welding process uses a gas flame to melt the edges of two adjoining surfaces. After the removal of the flame, the liquid metal cools to join the surfaces together. Gases used with oxygen or air are acetylene, MAPP gas, and hydrogen.
Cutting -- there are two common types of cutting done with welding equipment.
• Oxygen cutting heats metal with a gas flame - an oxygen jet increases the heat and blows away the molten metal.
• Arc cutting uses the high heat of an electric arc to melt a channel or hole in the metal.
Hot work is allowed only in areas that are or have been made fire-safe. Hot work may only be performed in either designated areas or permit-required areas.
A designated area is a specific area designed or approved for such work, such as a maintenance shop or a detached outside location that is of noncombustible or fire-resistive construction, essentially free of combustible and flammable contents, and suitably segregated from adjacent areas.
A permit-required area is an area made fire-safe by removing or protecting combustibles from ignition sources.
Hot work is not allowed:
• In sprinkle head buildings if the fire protection system is impaired.
• In the presence of explosive atmospheres or potentially explosive atmospheres ( e.g. on drums previously containing solvents).
• In explosive atmospheres that can develop in areas with an accumulation of combustible dust (e.g. grain silos).
Hot Works Procedures:
OSHA 29 CFR 1910.252 required fire prevention actions for welding/hot works.
Where practicable all combustibles shall be relocated at least 35 feet from the worksite.
Where relocation is impractical, combustibles shall be protected with flameproof covers, shielded with metal, guards, curtains, or wet down material to help prevent ignition of material.
Ducts, conveyor systems, and augers that might carry sparks to distant combustibles shall be protected or shut down. Where cutting or welding is done near walls, partitions, ceilings, or a roof of combustible construction, fire-resistant shields or guards shall be provided to prevent ignition.
If welding is to be done on a metal wall, partition, ceiling, or roof, precautions shall be taken to prevent ignition of combustibles on the other side, due to conduction or radiation of heat.
Where combustibles cannot be relocated on the opposite side of the work, a fire watch person shall be provided on the opposite side of the work.
Welding shall not be attempted on a metal partition, wall, ceiling, or roof having a covering nor on walls having combustible sandwich panel construction.
Cutting or welding on pipes or other metal in contact with combustible walls, partitions, ceilings, or roofs shall not be undertaken if the work is
Personal Protective Equipment
- Respirator, Welders Glasses, Welders Helmet, Hot work gloves, Leather cape, sleeves, apron, and leggings.
Identifying the hazards: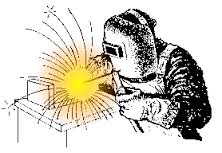
The first step in managing risks associated with welding processes is to identify all the hazards that have the potential to cause harm.
Welding and allied processes can have similar hazards and you can follow the same process
to identify hazards. For example, both welding and allied processes produce ultraviolet and
infra-red radiation which can cause burns, cancer, and blindness.
Potential hazards may be identified in a number of different ways including:
- conducting a walk-through assessment of the workplace observing the work and talking
to workers about how work is carried out.
- inspecting the materials and equipment that will be used during the welding process.
- reading product labels, SDSs, and manufacturer’s instruction manuals.
- talking to manufacturers, suppliers, industry associations, and health and safety specialists.
- reviewing incident reports.
Assessing the risks:
A risk assessment involves considering what could happen if someone is exposed to a hazard combined with the likelihood of it happening.
Under the Regulations a risk assessment is not mandatory for welding however, it is required for specific situations, for example when working in a confined space.
In some circumstances, a risk assessment will assist to:
- identify which workers are at risk of exposure.
-
determine what sources and processes are causing that risk.
- identify if and what kind of control measures should be implemented.
- check the effectiveness of existing control measures.
Risks will depend on various factors, including the:
- properties of the materials being welded.
- surface coating of the items being welded (for example whether they contain lead
or other toxic materials).
-
condition of the welding equipment.
- conditions under which welding is carried out (for example, confined spaces).
- skills, competence, and experience of the welder.
Different welding processes also influence the risk. For example, the risk of electric shock is lower using gas metal arc welding than manual metal arc welding because the open circuit voltages are lower, only direct current is used and the power is switched at the handpiece.
The following questions may help to assess the risk:
- In the event of exposure to the hazard, will the outcome be severe, moderate, or mild?
- How often, and for how long, will exposure to the hazard occur?
Controlling the risks:
The hierarchy of control measures
Some control measures are more effective than others. Control measures can be ranked from the highest level of protection and reliability to the lowest. This ranking is known as the hierarchy of control.
You must always aim to eliminate a hazard and associated risk first. For example, fabrications may be designed to include many pre-cast components or extruded shapes to eliminate the need to weld.
If this is not reasonably practicable, the risk must be minimised by using one or more of the following approaches:
- Substitution – replace a hazardous process or material with one that is less hazardous,
for example using submerged arc welding instead of flux-cored wire welding will reduce
the risk of exposure to radiation and fumes. In welding, such types of substitution are
not always practical or technically suitable.
- Isolation – removing the welder and nearby workers from the hazard or isolating or screening the hazard from the welder, for example ancillary processes like plasma cutting, gouging, grinding, fettling and guillotining can be carried out in specified areas away from general fabrication, to reduce risk of exposure to loud noise at the welding station.
- Engineering controls – use engineering control measures to minimize the risk, for example, ventilation systems to remove welding fumes.
If risk then remains, it must be minimized by implementing administrative controls, so far as is reasonably practicable. For example, if a welding process takes place in a very hot environment, allowing the welder to weld for a limited time followed by a suitable rest and cooling-off period will reduce the risk of heat exhaustion.
Any remaining risk must be minimized with suitable personal protective equipment (PPE). For example, if the welder has to stand on metallic surfaces that form part of the electric circuit it may become live. The use of rubber-soled boots will reduce the risk of electric shock.
Administrative control measures and PPE rely on human behavior and supervision. If used on their own, they tend to be least effective in minimizing risks.
A combination of these control measures may be required in order to adequately manage the risks with welding. You should check that your chosen control measure does not introduce new hazards.
Reviewing control measures:
The control measures that are put in place to protect health and safety should be regularly reviewed to make sure they are effective. This may involve, for example, atmospheric monitoring to measure the amount of welding fume in the welder’s breathing zone following introduction of fume extraction equipment. If the control measure is not working effectively it must be revised.
Common review methods include workplace inspection, consultation, testing and analysing records and data.
If problems are found, go back through the risk management steps, review your information and make further decisions about controlling the risk.
Electrical risks
Using electrical welding equipment involves a risk of electric shock or electrocution. Exposure
to electromagnetic fields is also a potential hazard for workers with some medical conditions.
Electric shock:
Electric shock may result in serious burns or death by electrocution. Electric shock or electrocution can occur through direct contact with the electrode, live parts, the work piece, or through contact with a device such as an unearthed cable or tool. The risk of electric shock can be exacerbated by moisture and high humidity.
Control measures
- Use fully insulated electrode holders. The holder should never be dipped into water to cool, or be placed on conductive surfaces.
- Prevent contacting electrodes or welding wire with bare hands when in the holder or welding gun (wear dry welding gloves), and make sure that holders or welding guns are never held under the armpits.
- Prevent holders or electrodes coming into contact with any other person.
- Check the working area does not have any potentially live structures, components or wet areas.
- Install a RCD.
- Inspect all equipment to check that it is in good condition prior to use,including power switches, terminals, connections, cables and insulation.
The working environment should be designed to minimise the risk of electric shock. For example, areas where welding is undertaken, can be insulated and air-ventilated to prevent workers from perspiring as perspiration is a conductor of electricity.
Table 1 below lists several ways to minimise the risk of electric shock when carrying out welding.
Electric arc welding produces strong electric and magnetic fields close to the power source and around the current-carrying cables. Electromagnetic fields can disrupt the operation of pacemakers, permanent defibrillators or other medical devices which could cause the heart to stop or slow down. A worker will not be aware of a magnetic field hazard unless a heart pacemaker or other device is behaving irregularly.
Electromagnetic fields can also occur wherever power is being generated and near transmission lines. Before work near these facilities begins, you should check with the electricity supply company to make sure work will not affect the supply of power or if there are any special precautions welders need to take when working in those areas.
Control measures:
- Use barriers to isolate people who are not directly involved in the welding process.
- Use signs indicating there are strong electromagnetic fields should be used to alert people to risks.
- Workers should not stand close to the power source or drape the welding cable around their body.
- Workers with pacemakers or other susceptible devices should substitute work that involves exposure to electromagnetic fields for another type of welding process, such as performing oxy-fuel welding instead of electric arc welding. Seek medical advice before exposing a worker wearing such a device to welding related electromagnetic fields.
Ventilation:
Ventilation can remove heat from the environment and reduce exposure to fumes &other atmospheric contaminants in the work area.
There are three main types of ventilation:
- local exhaust ventilation
- forced dilution ventilation.
- natural dilution ventilation.
The choice of ventilation system should take into account:
- the amount and type of fumes and contaminants produced.
- the proximity and location of the welding process relative to the ventilation system.
- the level of ventilation, natural or mechanical, both for the whole workplace and the welding area – this will also depend on screens and partitions which may restrict cross-flow at the work area.
- the proximity of the welder’s breathing zone to the fume source.
Local exhaust ventilation:
A local exhaust system may comprise the elements listed:
- a hood which captures the contaminant close to its point of generation.
- a duct system to move contaminant away from the work area.
- an air cleaning system to prevent pollution of the general atmosphere.
- an exhaust fan to provide air flow.
- a stack or other means of discharging the decontaminated air into the atmosphere.
Local exhaust ventilation systems should be designed to provide a minimum capture velocity at the fume source of 0.5m/second away from the welder. Inlets and outlets should be kept clear at all times. Air from a local exhaust ventilation system should not be re-circulated into the workroom. This air should be discharged into the outside air away from other work areas and away from air conditioning inlets or compressors supplying breathing air.
Examples of local exhaust ventilation suitable for welding operations include:
- fixed installations, such as side-draught or down-draught tables and benches, and partially or completely enclosed booths.
- portable installations, such as movable hoods that are attached to flexible ducts
(for example, see Figure 1).
- low volume high velocity fume extractors attached directly to the welding gun (for example, see Figure 2).
Forced dilution ventilation:
An elevated concentration of atmospheric contaminants can be diluted with a sufficient volume of clean air. Successful dilution ventilation depends not only on the correct exhaust volume but also on control of the airflow through the workplace. Although forced dilution ventilation systems are not as effective in controlling atmospheric contaminants as local exhaust ventilation systems, they may be useful to control minor emissions of low toxicity contaminants.
Figure 1: Local Exhaust ventilation in confined space welding
Figure 2: Fume extraction attached to the welding gun
Natural ventilation:
Natural ventilation should only be used for general comfort not as an engineered control measure for atmospheric contaminants and fumes.Natural ventilation can assist with the transfer ofcontaminants from the work area however it is not a reliable way of diluting or dispersing contaminants. For example, if a worker is working in a fixed position and the natural wind velocity is mild or wind is in a direction towards the worker, the worker may remain exposed to contaminants that have not been removed from the worker’s breathing zone.Personal protective equipment (PPE)
In most cases PPE must be worn by workers when welding to supplement higher levels of controls such as ventilation systems or administrative controls (see Figure 3).
Figure 3: Welder wearing welding helmet, dry leather welding gloves and leather apron
When PPE is worn by workers, it should not introduce other hazards to the worker, such as musculoskeletal injuries, thermal discomfort, or reduced visual and hearing capacity
The types of PPE recommended for use in welding are summarised in the following table:
SOURCE AND HEALTH EFFECT OF WELDING FUMES:
SOURCE AND HEALTH EFFECT OF WELDING GASES:
SOURCE AND HEALTH EFFECT OF ORGANIC VAPOURS AS A RESULT OF WELDING:
Du point -Hot work hidden hazard
Danger of hot work-H2SO4 tank explosion
Click the below link to know more details about Hot works
Click the below links for Different types of Hot work permits
Hot work-1 Hot work-2 Hot work-3 Hot work-4 Hot work-5
Hot work-6 Hot work-7 Hot work-8 Hot work-9 Hot work-10