Eye wash and safety shower:
Introduction: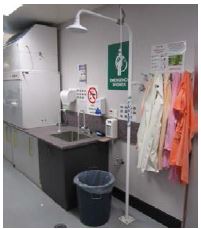
In today’s industries, many safety precautions and types of emergency equipment must be used to protect and ensure the health of employees. Although regulations and standards, personal protective equipment, and safety training are used, accidents still happen. Accidents involving hazardous chemicals can be especially severe. Employees who manufacture hazardous chemical products are at risk, of course. Hazardous chemicals can also affect people who work in food industries, or with cleaning solutions, and in manufacturing industries and service establishments.
Eyewashes and safety showers were developed in response to the increased use of hazardous chemicals. Eyewashes and safety showers are emergency systems used in both public and private industry to protect an employee from injury in case of contact with hazardous chemicals, chemical compounds or fire.
The four basic ways these safety systems are used (see Figure 1) include:
1. Dilution—diluting the chemicals that are on the skin or in the eyes to a nonharmful level.
2. Warming/cooling—warming or cooling the body or eyes because of a change in temperature due to chemical exposure.
3. Irrigation—flushing the chemicals out of the eyes or off the skin.
4. Extinguishment—putting out fires of clothing on the body.
The selection of emergency eyewash and shower equipment is often a complicated process. In addition to addressing design and engineering issues, specifiers must be aware of regulatory requirements and compliance standards. A common reference point when selecting emergency
equipment is ANSI/ISEA Z358.1, “Emergency Eyewash and Shower Equipment.” This standard is a widely accepted guideline for the proper selection, installation, operation and maintenance of emergency equipment.
To assist specifiers in understanding the provisions of this standard, Guardian Equipment has prepared this ANSI Compliance Checklist. In this Checklist, we have summarized and graphically presented the provisions of the standard. This Checklist can serve as a starting point for designing emergency eyewash and shower systems.
Legal requirements: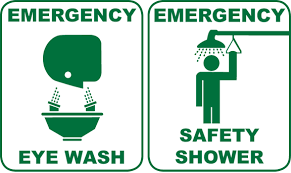
The Occupational Safety and Health Act of 1970 was enacted to assure that workers are provided with “safe and healthful working conditions.” Under this law, the Occupational Safety and Heath Administration (OSHA) was created and authorized to adopt safety standards and regulations to fulfill the mandate of improving worker safety.
OSHA has adopted several regulations that refer to the use of emergency eyewash and shower equipment. The primary regulation is contained in 29 CFR 1910.151, which requires where the eyes or body of any person may be exposed to injurious corrosive materials, suitable facilities for quick drenching or flushing of the eyes and body shall be provided within the work area for immediate emergency use.”
The types of equipment addressed by the ANSI standard include:
Definitions:
- Emergency shower. The emergency shower is “a unit that enables a user to have water cascading over the entire body.” This unit is used for general irrigation of the body and although it can be used to rinse the face, the unit is not meant for flushing of the eyes.
- Eyewash. The eyewash is a unit that supplies fluid to irrigate and flush the eyes.
- Personal eyewash. The personal eyewash is “a supplementary eyewash that supports plumbed units, self-contained units, or both by delivering immediate flushing for less than 15 minutes.” The major difference between self-contained or plumbed and personal eyewash equipment is that the self-contained or plumbed one must have at least a 15-minute supply of water while the personal units have less than a 15-minute supply. Because of this, the personal eyewash is used on the site for immediate flushing and while the victim is moved to another unit. Irrigation should continue once the victim reaches the other unit.
- Eye/face wash. This device is “used to irrigate and flush both the face and the eyes.”
- Hand-held drench hose. This arrangement is “a flexible hose connected to a water supply and used to irrigate and flush eyes, face, and body areas.” With this unit it may be necessary for another person to hold the hose to allow the victim to hold his or her eyes open.
- Combination unit. The combination unit combines a shower with an eyewash or eye/face wash, or with a drench hose, or with both into one assembly.
- Plumbed unit. A plumbed unit is permanently connected to a potable water source.
- Self-contained unit. A self-contained unit is not permanently installed and must be refilled or replaced after use.
Types of system:
Emergency showers and eyewash stations provide on-the-spot decontamination. They allow workers to flush away hazardous chemicals that can cause injury. The types of system found at the are detailed below:
Safety showers:
Safety showers also known as deluge showers are designed to flush the user's head and body. They should not be used to flush the user's eyes because the high rate or pressure of water flow could damage the eyes in some instances.
Safety showers are provided to wash off hazardous chemicals that may be splashed on the skin. Large volumes of water should be used to wash away contaminants and it may be necessary to remove contaminated clothing. Safety showers can also be used effectively in extinguishing clothing fires or for flushing contaminants off clothing.
Location: Install shower within 10 seconds (approximately 55 feet) of hazard, on the same level as hazard and with unobstructed travel path. Where strong acids or caustics are being handled, emergency showers should be located adjacent to the hazard, and an appropriate professional should be consulted for advice on the proper distance.
Identification: Identify shower location with highly visible sign. Area around shower shall be well-lit.
Water Temperature: Water delivered by shower shall be tepid (60-100°F).
Training: Instruct all employees in the location and proper use of emergency showers.
Maintenance/Inspection: Activate plumbed shower at least weekly. Inspect all emergency showers annually for compliance with standard.
Eyewash and eye/facewash stations:
Eyewash stations are located in laboratories and workshops to flush the eyes and face area if hazardous chemicals are splashed into them. In the event of hazardous chemicals splashing in the eyes, the stream of water from the spray should be directed into the eye for a period of 15 minutes before seeking medical attention.
A variety of eyewash units exist. Units are divided into installed/plumbed and portable units.
Plumbed units must have a 30-psi water supply. Flow is to be provided to both eyes simultaneously and at a velocity low enough to injury the eyes. Plumbed and self-contained units must perform as follows:
- Eyewash: 0.4 gpm for 15 minutes;
- Eye/face wash: 3 gpm for 15 minutes
Location: Install eye/face wash within 10 seconds (approximately 55 feet) of hazard, on the same level as hazard and with unobstructed travel path. Where strong acids or caustics are being handled, emergency eye/face wash should be located adjacent to the hazard, and an appropriate professional should be consulted for advice on the proper distance.
Identification: Identify eye/face wash location with highly visible sign. Area around eye/face wash shall be well-lit.
Water Temperature: Water delivered by eye/face wash shall be tepid (60-100°F).
Training: Instruct all employees in the location and proper use of emergency eye/face wash.
Maintenance/Inspection: Activate plumbed eye/face was at least weekly. Inspect all emergency eye/face wash annually for compliance with standard.
The difference between the eye and eye/face wash is the size of the nozzle and spray pattern. The unit has to be installed between 33 inches and 45 inches above ground level and 6 inches away from the wall. There must be enough room to allow the eyelids to be held open with the hands while the eyes are in the flushing water stream.
Since the nozzles face upward to operate properly, dust and other contaminants could fall into the openings clogging them or providing a breeding area. Therefore, the nozzles have to be protected in such a way as to not require a separate movement to remove them when the unit is activated.
Combination units:(Safety station)
This name refers to equipment that shares a common plumbing fixture. Any of the fixtures such as shower, eyewash, and eye/face wash or drench hose may be in this combination, but most commonly it refers to a shower and an eyewash station.
A combination unit has the ability to flush any part of the body or all of the body. It is the most protective device and should be used wherever possible. This unit is also appropriate in work areas where detailed information about the hazards is lacking, or where complex, hazardous operations involve many chemicals with different properties. A combination unit is useful in situations where there are difficulties handling a worker who may not be able to follow directions because of intense pain or shock from an injury.
Location: Install safety station within 10 seconds (approximately 55 feet) of hazard, on the same level as hazard and with unobstructed travel path. Where strong acids or caustics are being handled, emergency safety station should be located adjacent to the hazard, and an appropriate professional should be consulted for advice on the proper distance.
Identification: Identify safety station location with highly visible sign.Area around drench hose shall be well-lit.
Water Temperature: Water delivered by safety station shall be tepid (60-100°F).
Training: Instruct all employees in the location and proper use of emergency safety station.
Maintenance/Inspection: Activate plumbed drench hose at least weekly. Inspect all emergency safety station annually for compliance with standard.
Drench hoses:
Hand-held drench hoses are supplemental devices that are designed to support emergency showers and eyewashes, but cannot be used instead. They consist of a flexible hose connected to a flushing fluid supply and used to provide fluid to irrigate and flush face and body areas. Drench hoses are useful in cases where the user is in the prone position or to reach areas of the face and body inaccessible to the fixed stream of a deluge shower or eye wash unit. They should provide a flow rate of at least 3 gpm for 15 minutes.
Location: Install drench hose within 10 seconds (approximately 55 feet) of hazard, on the same level as hazard and with unobstructed travel path. Where strong acids or caustics are being handled, emergency drench hose should be located adjacent to the hazard, and an appropriate professional should be consulted for advice on the proper distance.
Identification: Identify drench hose location with highly visible sign. Area around drench hose shall be well-lit.
Water Temperature: Water delivered by drench hose shall be tepid (60-100°F).
Training: Instruct all employees in the location and proper use of emergency drench hose.
Maintenance/Inspection: Activate plumbed drench hose at least weekly. Inspect all emergency eye drench hose annually for compliance with standard.
Eyewash bottles: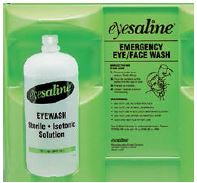
Personal eyewash equipment can be used to support plumbed or self-contained eyewashes, but may not replace them. They are regarded as secondary or supplemental eyewash stations.
They are portable and permit immediate flushing of contaminants or small particles. The main purpose of eyewash bottles is to supply immediate flushing until the injured person can get to a primary eyewash station that provides a full 15 minute flow. These personal eyewash stations should be placed in proximity to a worker's area for immediate flushing.
Eyewash bottles can be very difficult for the user to handle, especially when alone and when both eyes have been exposed. (e.g., holding the eyelids open while handling the unit is awkward). Also, one bottle cannot flush both eyes simultaneously. Since the fluid supply lasts for only a short period of time, the bottle may not able to wash the eyes sufficiently.
Location of emergency equipment: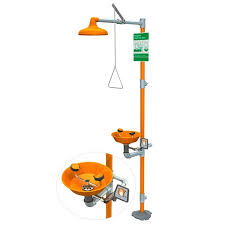
In general, the ANSI standard provides that emergency equipment be installed within 10 seconds walking time from the location of a hazard (approximately 55 feet) .The equipment must be installed on the same level as the hazard (i.e. accessing the equipment should not require going up or down stairs or ramps). The path of travel from the hazard to the equipment should be free of obstructions and as straight as possible.
However, there are certain circumstances where these guidelines may not be adequate. Previous versions of the standard expressly provided that, where workers are handling particularly strong acids, caustics or other materials where the consequences of a spill would be very serious, emergency equipment should be installed immediately adjacent to the hazard. Although of the 2014 standard briefly reviews the proper location of emergency equipment under such scenarios, we still believe the previous versions of the standard to be correct.
Water Temperature:
The 2014 version of the standard states that the water temperature delivered by emergency equipment should be ‘tepid.’ Tepid is defined to be between 60°F (16°C) and 100°F (38°C). However, in circumstances where a chemical reaction is accelerated by flushing fluid temperature, a facilities
safety/health advisor should be consulted to determine the optimum water temperature for each application.
The delivery of tepid water to emergency equipment may raise complicated engineering issues. At a minimum, it generally involves providing both hot and cold water to the unit, and then installing a mixing valve to blend the water to the desired temperature. Guardian offers a variety of mixing
valves and turnkey, recirculating tempering systems to provide tempered water. Please contact our office for further information.
Shut off valves:
Plumbed emergency equipment must be connected to a potable water supply line. It may be advisable to install a shut off valve on the water line, upstream of the unit, to facilitate maintenance of the equipment. If a shut off valve is installed, provision must be made to prevent unauthorized closure of the shut off valve. Such provision can include removing the handle of the shut off valve or locking the valve in the open position. Only maintenance personnel should be authorized to place a handle on or unlock the valve.
Corrosion resistance:
Once connected to a water supply line, water will enter the emergency equipment and stand in the unit up to the valve(s). When activated, water will flow through the entire unit. Therefore, the unit must be constructed of materials that will not corrode when exposed to water for extended periods
of time.
Materials that are considered acceptable for this purpose include brass, galvanized steel and many types of plastics (ABS, nylon, etc.). However, these materials may not provide durable service when exposed to harsh industrial conditions, may deteriorate in direct sunlight or be subject to other limitations. Therefore, for maximum durability, the following materials should also be considered:
- Epoxy coated galvanized steel
- Epoxy coated brass
- Stainless steel
- PVC
Freezing:
There are many applications where emergency equipment must be installed in areas that are subject to freezing conditions. Such areas may include any type of outdoor area (bulk material handling facility, tank farm, etc.), as well as some interior areas (loading docks, low temperature facilities, etc.). In these cases, the emergency equipment must be protected against freezing. Equipment that is designed and manufactured to be freeze-resistant should be installed. There are a number of different types of freeze-resistant equipment, including:
- Units that have a temperature actuated bleed valve that permits water to flow through the unit when the temperature drops below freezing. These units are generally used only where the possibility of freezing is very infrequent.
- Units on which the valve is mounted behind a wall or buried below the frost line and is remote activated.
- Combination units that are electrically heated (heattraced) and insulated.
- Units that have a heated enclosure to fully contain and protect both the equipment and the user.
Disposal of water: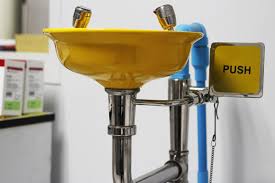
The standard does not include any specific provisions regarding the disposal of waste water. However, designers must give consideration to where waste water will go. In particular, care must be taken that waste water not create a hazard (i.e. by creating a pool in which someone might slip) or freeze.
Emergency response:
Simply installing emergency equipment is not sufficient to assure worker safety. Employees must be trained in the location of emergency equipment and in its proper use. Emergency equipment must be regularly maintained (including weekly activation of the equipment) to assure that it is in working order and inspected at least annually for compliance with the standard. Most importantly, employers
should develop a response plan to be used in the event that an accident does occur. The focus of the response plan should be to provide assistance to the injured worker as quickly as possible.
Training:
All workers/students who might be exposed to chemical splash must be trained by their department or lab supervisor as part of their induction on the following:
The specific location of the units serving that area.
- How to properly activate and use the specific type of system.
- Use of the eyewash station in the event of an eye injury - Individuals should be instructed to hold the eyelids “open” and roll the eyeballs continuously so fluid will flow on all surfaces of the eye and under the eyelid seek medical attention. For specific treatment for the chemical concerned – refer to the SDS.
- Use of the safety shower in the event of a chemical spill onto their body. Individuals should be instructed to remove all contaminated clothing including footwear and socks/stockings while under the shower when cross contamination has occurred. Have someone assist with clothing removal when possible. An assistant may use a fire blanket or uncontaminated article of clothing as a shield to provide privacy for someone who needs to remove their clothes while under an emergency shower, and for body coverage while seeking medical attention.
- Flush body for a minimum of 15 minutes, seek medical attention. For specific treatment for the chemical concerned – refer to the SDS.
It should never be assumed that workers are already aware of the proper procedures. Written instructions should be made available to all workers and others and posted beside the emergency shower and eyewash station. Part of the instructional process should include a "hands-on" drill on how to find equipment.
The wearing of contact lenses can be dangerous because chemicals can become trapped under a contact lens. Any delays caused by removing contact lenses in order to rinse eyes could result in injury. Training should include instruction in contact lens removal.
Frequency of testing:
It is important to understand that routine inspection involving “activation or flushing” and “flow testing” are different procedures that are performed by different people and occur at different intervals.
Routine inspection:
AS 4775-2007 states that plumbed showers and eyewash equipment “shall be activated weekly for a period long enough to verify operation and ensure that flushing fluid is available”. This weekly interval may be varied on the basis of a documented risk assessment.
The standard notes that the intent behind this is to ensure that “there is a flushing fluid supply at the outlet of the device, to clear the supply line of any sediment build-up that could prevent fluid from being delivered to the outlet of the device and to minimize microbial contamination due to sitting water.”
The frequency of testing practice varies across Australian universities with most conducting their routine inspections either weekly or monthly. Based on risk assessment, a monthly inspection routine has been prescribed as adequate to ensure that safety showers and eyewash stations supply clean, potable water and are in proper working order. However, faculties / departments may deem that in situations where they are working with very corrosive chemicals with high splash potential, a weekly or even daily check would be advisable.
Local routine inspection and testing:
Routine inspections are most effectively conducted by two people.
Check all associated equipment and fittings for serviceability and ensure clear access to the shower/eyewash station.
Depending on the style of test sock, one person will position the test sock under or around the shower head (Figure 2) or eyewash station (Figure 4). A step ladder may sometimes be necessary to get within reach the showerhead.
Place the other end of the test sock inside the bucket (refer Figure 3).
The second person then operates the shower / eyewash station release valve (refer Figure 2). The valve is designed so that the flushing liquid flow remains on without the use of the operators’ hands.
Equipment should be activated for a period long enough to verify operation and ensure that flushing fluid is available and clean. This flushing helps clean out any rust, scale deposits, or bacteria that may accumulate and cause additional injury.
After evidence of clear water flow, shut off valve to terminate the test. Drain the bucket and clean up any water spills that may cause slip hazards.
Figure 2 -Testing shower Figure 3 -Testing eye wash station
Figure 4 -Testing socks
Routine inspection checklist:
Safety showers:
The routine inspection should include, at a minimum, the following:
- Ensure that access to the shower is clear of any obstructions.
- Ensure the shower is within 10 seconds of hazard.
- Visually inspect the shower to ensure that there are no broken parts, pipe damage, leakage etc. This should be done prior to testing in order to avoid further damage to the unit and risk of injury to users and yourself.
- Activate unit. Ensure that the water flow is effective and continuous.
- Operate the shower for long enough to verify operation and relieve the unit of any rust and other pipe build-up. Flush the unit until the water runs clear.
- Check that the unit remains activated without the use of the operator’s hands. Valve actuator must stay on unless manually turned off and must activate water flow in one second or less.
- Ensure each shower has a highly visible emergency sign.
- Ensure that problems identified during the inspection are reported immediately.
- Document test with dates and initials on the testing record located either adjacent to the unit or in a central area where several units are located on the same floor.
Eyewash units:
The routine inspection should include, at a minimum, the following:
- Verify that protective eyewash covers are properly positioned, clean, intact and operate properly when activated.
- Check that aerators are in good condition and free of corrosion.
- Activate eyewash unit - flush pipes: check that the spouts are clean and that the water flow is effective and continuous. Operate the eyewash for long enough to verify operation and ensure that flushing fluid is available not injurious to the user's eye or face.
- The unit must deliver low-pressure “soft” flow to both eyes so it does not injure the open eyes.
- Controlled flow of flushing fluid must be provided to both eyes simultaneously.
Flushing water: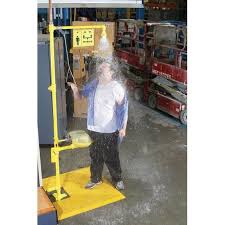
- Water must be able to maintain its flush for a minimum of 15 minutes. If there are requirements for longer flushing than this, shall be clearly indicated by prominent signage.
- Water should be tepid (between 15o and 35oC). If there is a possibility of water freezing or boiling (over 38oC) adequate protection must be introduced.
- Safety showers and eyewash units must meet the minimum flow rate required .
- Eyewash units need to be capable of washing both eyes simultaneously at a velocity low enough to be non-injurious to the eyes.
- If shut off valves are installed for maintenance purposes, they need to be secure from any unauthorised shut off.
Minimum flow rates:
All units should be plumbed at 210kPa and must be able to maintain a period of not less than 15 minutes.
- Showers 75.7 litres per minute
- Eye/face wash 11.4 litres per minute
- Drench hose 11.4 litres per minute
- Eyewash 1.5 litres per minute
Rates can be tested with a flow meter or by other means of measuring flushing fluid flow such as timing to fill a bucket. Results are to be recorded on the ‘Maintenance Checklist - Safety shower flow rate’.
Signage:
The location of each emergency shower or eyewash station shall be well illuminated and be identified with a highly visible sign complying with AS1319 – 1994 Safety Signs for the Occupational Environment visible throughout the area served by the equipment. The sign should be in the form of a symbol that does not require workers to have language skills to understand it. The location should be well lit.
Click the below link to download the safety shower, eye wash check sheet
Safety shower, eye wash and drench hose - Safety check sheet