Rigging hardwares-Blocks:
Introduction:
Blocks are used to reverse the direction of the rope in the tackle. Blocks take their names from—
- The purpose for which they are used.
- The places they occupy.
- A particular shape or type of construction.
Types of Blocks:
Blocks are designated as single, double, or triple, depending on the number of sheaves.
- Snatch Block
- Traveling Block
- Tackle Blocks
Snatch Block:
This is a single sheave block made so that the shell opens on one side at the base of the hook to permit a rope to be slipped over the sheave without threading the end of it through the block. Snatch blocks ordinarily are used where it is necessary to change the direction of the pull on the line. The following figure-1 show snatch block and figure-2 show typical components of snatch block.
Figure-1 Figure-2
Traveling Block:
A traveling block is attached to the load that is being lifted and moves as the load is lifted. The following figure-3 show traveling block and figure-4 show typical components of traveling block.
Figure-3 Figure-4
Utility or standing blocks:
This block is fixed to a stationary object. The following figure-5 show utility block and figure-6 show typical components of standing block.
Figure-5 Figure-6
Rolling block:
The following figure-7 show rolling block and figure-8 show typical components of rolling block.
Figure-7 Figure-8
Leading Blocks:
Blocks used in the tackle to change the direction of the pull without affecting the system are called leading blocks (see Figure 9). In some tackle systems, the fall line leads off the last block in a direction that makes it difficult to apply the motive force required. A leading block is used to correct this. Ordinarily, a snatch block is used as the leading block.
This block can be placed at any convenient position. The fall line from the tackle system is led through the leading block to the line of most direct action.
Firgure-9 (Use of leading block)
Reeving blocks:
To prepare blocks for use, reeve, or pass a rope through, it. To do this, lay out the blocks on a clean and level surface other than the ground to avoid getting dirt into the operating parts, Figure-10 shows the reeving of single and double blocks. In reeving triple blocks, it is imperative that you put the hoisting strain at the center of the blocks to prevent them from being inclinedunder the strain (see Figure -11). If the blocks do incline, the rope will drag across the edges of the sheaves and the shell of the block and cut the fibers. Place the blocks so that the sheaves in one block are at right angles to the sheaves in the other block. You may lay the coil of rope beside either block. Pass the running end over the center sheave of one block and back to the bottom sheave of the other block. Then pass it over one of the side sheaves of the first block. In selecting which side sheave to pass the rope
Figure-10 Reeving single and double blocks
over, remember that the rope should not cross the rope leading away from the center sheave of the first block. Lead the rope over the top sheave of the second block and back to the remaining side sheave of the first block. From this point, lead the rope to the center sheave of the second block and back to the becket of the first block. Reeve the rope through the blocks so that no part of the rope chafes another part of the rope.
Figure-11 Reeving triple blocks
Twisting of Blocks: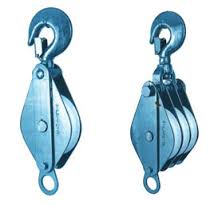
Reeve blocks so as to prevent twisting. After reeving the blocks, pull the rope back and forth through the blocks several times to allow the rope to adjust to the blocks. This reduces the tendency of the tackle to twist under a load. When the ropes in a tackle system become twisted, there is an increase in friction and chafing of the ropes, as well as a possibility of jammingthe blocks. When the hook of the standing block is fastened to the supporting member, turn the hook so that the fall line leads directly to the leading block or to the source of motive power. It is very difficult to prevent twisting of a traveling block. It is particularly important when the tackle is being used for a long pull along the ground, such as in dragging logs or timbers.
Antiwisting Devices:
One of the simplest antitwisting devices for such a tackle is a short iron rod or a piece of pipe lashed to the traveling block (see Figure -12). You can lash the antitwisting rod or pipe to the shell of the block with two or three turns of rope. If it is lashed to the becket of the block, you
should pass the rod or pipe between the ropes without chafing them as the tackle is hauled in.
Figure-11 Antitwisting pipe or rod
Types and materials: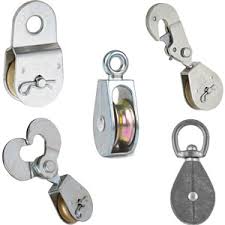
Types:
(a) Types include tackle, utility, rolling, and snatch blocks (see Fig. 1 to 2).
(b) Load fittings on rigging blocks may include hooks, eyes, swivels, yokes, bails, shackles, and pins.
(c) Rigging blocks other than those detailed in this Chapter shall be used in accordance with recommendations of the manufacturer or a qualified person.
Materials:
(a) The rigging block shall have sufficient ductility to permanently deform before losing the ability to support the load at the temperatures that the manufacturer has specified for use.
(b) The shell or side plates shall be metal, wood, or synthetic.
(c) The sheave(s) shall be metal or synthetic.
(d) The load bearing straps and fitting(s) shall be made of metal.
PROOF TEST:
Proof Test Requirements:
(a) Rigging blocks are not required to be proof tested unless specified by the purchaser.
(b) If proof tested, a rigging block shall be inspected after the test for the conditions stated in para.
Proof Load Requirements:
The proof load for a rigging block shall be a minimum1.5 and a maximum of 2 times the rated load unless approved by the manufacturer or a qualified person.
IDENTIFICATION:
Marking:
Each new rigging block shall be marked by the manufacturer to show:
(a) name or trademark of manufacturer
(b) rated load
(c) rope size(s)
Maintenance of Identification:
Rigging block identification should be maintained by the user so as to be legible throughout the life of the block.
EFFECTS OF ENVIRONMENT:
Temperature:
When rigging blocks are to be used at temperatures above 150°F (66°C) or below 0°F (18°C), the rigging block manufacturer or a qualified person should be consulted.
Chemically Active Environments:
Chemically active environments such as caustic or acid substance or fumes can affect the strength, operating characteristics, or both, of rigging blocks. The rigging block manufacturer or a qualified person should be consulted when rigging blocks are used in chemically active environments.
Storage & Work Environments: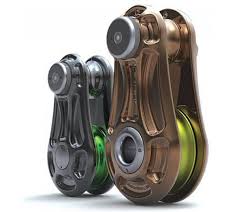
(a) Rigging blocks should be stored in an area where they will not be subjected to damage, corrosive action, or extreme temperatures.
(b) If extreme temperatures or chemically active environments are involved, the guidance provided shall be followed.
Cautions to Personnel:
(a) All portions of the human body shall be kept from between the rigging block, its running lines, the load, and any other rigging during the lift.
(b) Personnel should stand clear of the suspended load.
(c) Personnel shall not ride rigging blocks.
Design factor:
The design factor for rigging blocks shall be a minimum of 4.
Rated loads:
Rated load shall be in accordance with the recommendation of the rigging block manufacturer. The terms “rated capacity” and “working load limit” are commonly used to describe rated load.
Note: The block rated load is the maximum load applied to the primary load fitting, not the line pull (see Fig. 12).
Figure-12
Example: Load 1,000 lb
Line Pull: 1,000 lb 2 500 lb
Load Block “C” 500 lb 2 1,000 lb
(line pull factor for 0 deg angle)
Load Block “D” 500 lb 1.87 500 lb 1,435 lb
(line pull factor for 40 deg angle dead-end load)
Load Block “E” 500 lb 0.84 420 lb
(line pull factor for 130 deg angle)
Load Block “F” 500 lb 1.41 705 lb
(line pull factor for 90 deg angle)
Training:
Rigging block users shall be trained in the selection, inspection, cautions to personnel, effects of environment, and rigging practices as covered by this Chapter.
Inspection, repair and removal: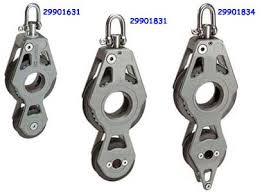
Initial Inspection:
Prior to use, all new, altered, modified, or repaired rigging blocks shall be inspected by a designated person to verify compliance with the applicable provisions of this Chapter. Written records are not required.
Frequent Inspection:
(a) A visual inspection shall be performed by the user or other designated person each shift before the rigging block is used. Semi-permanent and inaccessible locations where frequent inspections are not feasible shall have periodic inspections performed.
(b) Conditions such as those listed or any other condition that may result in a hazard, shall cause the rigging block to be removed from service. Rigging blocks shall not be returned to service until approved by a qualified person.
(c) Written records are not required.
Periodic Inspection: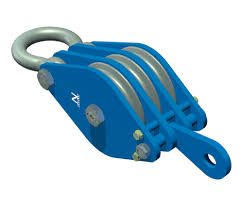
(a) A complete inspection of the rigging block shall be performed by a designated person. The hardware shall be examined for conditions such as those listed and a determination made as to whether they constitute a hazard.
(b) Periodic Inspection Frequency. Periodic inspection intervals shall not exceed one year. The frequency of periodic inspections should be based on
(1) frequency of use
(2) severity of service conditions
(3) nature of lifts being made
(4) experience gained on the service life of hardware used in similar circumstances
(5) Guidelines for the time intervals are
(a) normal service – yearly
(b) severe service – monthly to quarterly
(c) special service – as recommended by a qualified person
(c) Written records are not required.
Removal Criteria:
Rigging blocks shall be removed from service if conditions such as the following are present and shall only be returned to service when approved by a qualified person:
(a) missing or illegible identification
(b) misalignment or wobble in sheaves
(c) excessive sheave groove corrugation or wear
(d) loose or missing nuts, bolts, cotter pins, snap rings, or other fasteners and retaining devices
(e) indications of heat damage, including weld spatteror arc strikes
( f ) excessive pitting or corrosion
(g) bent, cracked, twisted, distorted, stretched, elongated, or broken load bearing components
(h) excessive wear, nicks, or gouges
(i) a 10% reduction of the original or catalog dimension at any point
(j) excessive damage to load bearing threads
(k) evidence of unauthorized welding or modifications
(l) for hooks, the removal criteria specified in B30.10
(m) for shackles, the removal criteria specified in B30.26
(n) other conditions, including visible damage that cause doubt as to the continued use of the rigging block
Repairs and Modifications: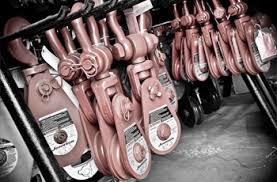
(a) Repairs, alterations, or modifications shall be as specified by the rigging block manufacturer or a qualified person.
(b) Replacement parts, such as pins, hooks and sheaves, shall meet or exceed the original equipment manufacturer’s specifications.
Operating Practice:
Rigging Block Selection:
(a) Rigging blocks having suitable characteristics for the application and environment shall be selected in accordance with the recommendations of the rigging block manufacturer or a qualified person.
(b) The rated load of the rigging block shall not be exceeded.
NOTE: The included angle formed between the load lines affects the load on the block. As the included angle decreases, the load increases in the rigging block .
(c) Rigging blocks that appear to be damaged shall not be used until inspected and accepted as usable under removal criteria.
(d) The minimum D/d ratio between the sheave pitch diameter and the wire rope diameter is 6.
Rigging Practices:
(a) The rigging block components shall be fully engaged, with all fasteners and retaining devices in place and in good working order before use. Alterations or modifications shall comply repair and modification.
(b) Contact with sharp edges that could damage the rigging block should be avoided.
(c) Shock loading should be avoided.
(d) The load applied to the rigging block should be in-line with the sheave and load fitting(s) to prevent side loading of the block.
(e) Ensure the rope is in the sheave groove when the rigging block begins to take load.
( f ) The line load multiplied by the block load factor shall not exceed the rated load of the rigging block (see Fig. 12).
(g) Rigging blocks should not be dragged on an abrasive surface.
(h) Load line fittings shall not contact the rigging block sheave(s).