Rigging Hardware-Eye bolts:
Overview:
One of the most commonly used items of lifting gears have severe limitation in usage and a high level of accidents occurs as a result of misuse. Eyebolts are used in a wide variety of applications to provide lifting points on loads. Sometimes the hole they are screwed into is there specifically for the eyebolt. Alternatively a hole that is primarily intended for some other purpose, such as stud, can be utilized.
Traditionally eyebolts were often fitted to their load and lift in place for life, being regarded s part of the load, however modern practice is to treat detachable lifting point as lifting accessories. As such most the countries require that they are periodically inspected or thoroughly exanimated. Therefore good practice is to remove eyebolts, plug the holes and put the eyebolts into storage until needed . This often considerably recuses the quantity required and opens up their options.
In general, the best alternative to eyebolts are the modern lifting points, swivel links and hoist rings. Although there is not a specific standard for theses, several reputable manufactures including Crosby, RUD and Yoke, who make them to their own designs. These new generation lifting points offer advanced engineering and increased load capacities over standard eyebolts.
Lifting safety offers a great variety of styles are offered to try to ensure that we have a fitting to suit our customer's applications. Stainless steel lifting eyebolts are used where there is the potential of corrosion contamination or failure caused by corrosion. We offer different types of stainless steel eyebolts including stainless steel swivel eye bolts with links that will automatically adjust to the direction of the load. Other lifting eye bolts in this category include specially manufactured bolt-on eyebolt plates available for permanent or temporary installation for fitting to an overhead beam to create a lifting point or fall arrest anchorage point. We also offer in this category of the shop ISO container lifting eyes are also referred to as container lifting lugs designed to connect to the top, side, or bottom of ISO shipping Containers (International Organization for Standardization)
Definitions:
Eyebolts used for hoisting shall be fabricated from forged carbon or alloy steel and shall have sufficient ductility to permanently deform before losing the ability to support the load at
temperatures at which the manufacturer has specified for use.
Each eyebolt shall be marked to show:
1. Name or trademark of the manufacturer.
2. Size or rated load.
3. Grade for alloy eyebolts.
Eyebolts shall have a minimum design factor of 5:1.
Only shouldered eyebolts shall be used for rigging hardware, except when prohibited by the
configuration of the item to be lifted. Where non-shouldered eyebolts are required, they shall only be used in vertical pulls or in rigging systems that are designed and approved by a qualified person.
When eyebolts cannot be properly seated and aligned, a steel washer or spacer with the smallest inside diameter that will fit the eyebolt shank may be used to put the plane of the eye in the direction of the load when the shoulder is seated. The washer or spacer shall not exceed one thread pitch in thickness or as recommended by the manufacturer. Eyebolts shall be tightened or otherwise secured against rotation during the lift.
Only shouldered eyebolts shall be used for angular loading. The shoulder shall be securely tightened against the load and the eye shall be aligned with the direction of the loading. The working load limit shall be reduced as recommended by the manufacturer.
Types of Eyebolts:
There are four specialized types of eyebolts.
-
Forged eyebolts are forged instead of formed. These one-piece fasteners offer higher load ratings.
-
Screw eyes are screws with a head shaped into a loop or eye. They are often used in lifting and rigging applications, or to guide wire or cable.
-
Shoulder eyebolts have a shoulder under the eye. Typically, the shoulder is installed flush with the mounting surface.
-
Thimble eyebolts are designed with an opening that acts as a thimble for wire or rope to minimize wear.
-
Pivoting eyebolts are designed to pivot 180°. The base of a swiveling eyebolt is designed to swivel 360°.
Shouldered:
Used for vertical and angular lifts; when used for angular lifts the Safe Working Load (SWL) is to be downrated. Angles less than 45 degrees are prohibited. The Shoulder must be flush with the surface and screw.
Unshouldered - for vertical lies only, angular lifts will bend threaded shaft.
Shouldered eyebolts shall be used for all applications, except where it is not possible due to the configuration of the item. When unshouldered eyebolts are used, nuts, washers, and drilled plates shall not be used to make shouldered eyebolts. Swivel eyebolts are also available in the tool crib.
Eyebolts shall have a minimum thread engagement between the eyebolt and its tapped hold of 1-1 /2 times the diameter of thread engagement. Nuts on through-eyebolts shall be self-locking types. The shoulders shall seat uniformly and snugly against the surface on which they bear.
Specifications:
Specifications for eyebolts include:
-
Maximum load capacity - The maximum load which an eyebolt can handle.
-
Shank length - For fully-threaded eyebolts, shank diameter equals the thread length.
-
Threaded length
- Eye inside diameter (ID)
-
Eye section diameter of eye thickness
-
Total weight
Material and Finish:
Eyebolts differ in terms of material and finish. Plastic eyebolts and rubber eyebolts may be suitable for some applications. Metallic eyebolts can be made of materials including:
-
Aluminum
-
Brass
-
Bronze
-
Steel
-
Hardened steel
-
Stainless steel
-
Titanium
-
Proprietary alloys
In terms of finish, eyebolts are often anodized, galvanized, or plated with gold, silver, tin, or zinc. Black oxide is an eyebolt coating that causes virtually no dimensional change. Phosphate coatings provide corrosion resistance and a better surface for the adhesion of primers and paints. Eye bolts with zinc chromate finishes are also available.
Operation Practices:
1) The size of the hole shall be checked for the proper size of eyebolt prior to installation. The condition of the threads in the hole shall be checked to ensure the eyebolt will secure, and the shoulder can be brought to a snug and uniformly engaged seat.
2) When installed, the shoulder of the eyebolt must be flush with the surface. When eyebolts cannot be properly seated and aligned with each other, properly sized washers or shims may be
inserted under the shoulder to facilitate the eyebolts being tightened and aligned (firgure-1). However, minimum thread engagement must be maintained.
(firgure-1)
3) Angular loading of eyebolts should be avoided. Angular loading occurs in any lift in which the lifting force is applied at an angle to the centerline of the shank of the eyebolt. Angular loading of the
eyebolt less than 45 degrees shall be prohibited. The eyebolt loading shall never exceed the values.
4) When more than one eyebolt is used in conjunction with multiple-leg rigging, it is recommended that spreader bars, lifting yokes, or lifting beams be utilized to eliminate angular loading. When these
cannot be used, the values must not be exceeded.
5) To keep bending forces on the eyebolt to a minimum, the load shall always be applied in the plane of the eye, never in the other direction (figure-2).
(figure-2)
6) If the hook will not go completely into the eyebolt, a shackle will be used to avoid hoot tip loading.
7) Slings shall not be reeved through the eyebolt or reeved through a pair of eyebolts (firgure-3). Only one leg should be attached to each eyebolt. Reeving slings through eyebolts adds greater
load tension in the eyebolt than normally calculated by using the sling angle.
(firgure-3)
INSPECTIONS:
a. Initial Inspection: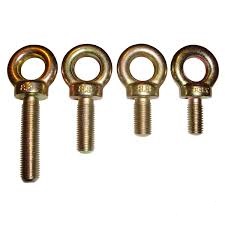
1. Prior to use, all new, altered, modified, or repaired eyebolts shall be inspected by a designated person to verify compliance with the applicable provisions of this chapter. Written records are not required.
b. Frequent Inspection:
1. A visual inspection shall be performed by the user or other designated person each shift before the eyebolt is used. Semipermanent and inaccessible locations where frequent inspections are not feasible shall have periodic inspections performed.
2. Conditions such as those listed in section removal criteria or any other condition that may result in a hazard shall cause the eyebolt to be removed from service. Eyebolts shall not be returned to service until approved by a qualified person.
3. Written records are not required.
c. Periodic Inspection:
1. A complete inspection of the eyebolt shall be performed by a designated person. The eyebolt shall be examined for conditions such as those listed in section removal criteria and a determination made as to whether they constitute a hazard.
2. Periodic inspection intervals shall not exceed one year. The frequency of periodic inspections should be based on:
Frequency of use.
- TheSeverity of service conditions.
- Nature of lifts being made.
- Experience gained on the service life of eyebolts used in similar circumstances.
3. Guidelines for the time intervals are:
i. Normal service – yearly.
ii. Severe service – monthly to quarterly.
iii. Special service – as recommended by a qualified person.
4. Written records are not required.
REMOVAL CRITERIA:
Eyebolts shall be removed from service if damage such as the following is visible, and shall only be
returned to service when approved by a qualified person:
a. Missing or illegible manufacturer’s name or trademark and/or rated load identification.
b. Indications of heat damage including welding spatter or arc strikes.
c. Excessive pitting or corrosion.
d. Bent, twisted, distorted, stretched, elongated, cracked, or broken load-bearing components.
e. Excessive nicks or gouges.
f. A 10% reduction of the original or catalog dimension at any point around the body or pin.
g. Excessive thread damage or wear.
h. Evidence of unauthorized welding or modification
i. Other conditions, including visible damage, that cause doubt as to continue use.
REPAIRS: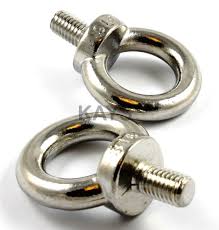
a. Repairs, alterations, or modifications shall be as specified by the eyebolt manufacturer or a
qualified person.
b. Replacement parts shall meet or exceed the original equipment manufacturer’s specifications.
EFFECTS OF ENVIRONMENT
a. When alloy steel eyebolts are to be used at temperatures above 400°F (204°C) or below- 40°F (-40°C), the eyebolt manufacturer or a qualified person should be consulted.
b. Carbon steel eyebolts shall not be used at temperatures above 275°F (135°C) or below 30° F (-1°C) unless approved by manufacturer or a qualified person.
c. The strength of eyebolts can be affected by chemically active environments such as caustic or acid substances or fumes. The eyebolt manufacturer or a qualified person should be consulted before eyebolts are used in chemically active environments.
Eye bolt identification markings:
Shoulder Nut Eye Bolt – Installation for In-Line and Angular Loading:
A.The threaded shank must protrude through the load sufficiently to allow full engagement of the nut
B.If the eye bolt protrudes so far through the load that the nut cannot be tightened securely against the load, use properly sized washers to take up the excess space BETWEEN THE NUT AND THE LOAD
C.Place washers or spacers between nut and load so that when the nut is tightened securely, the shoulder is secured flush against the load surface
D.Thickness of spacers must exceed this distance between the bottom of the load and the last thread of the eye bolt
Regular Nut & Shoulder Nut Eye Bolt - Installation for In-line Loading with a tapped hole:
- More than one eye bolt diameter of threads, only (1) nut is required
- Tighten hex nut securely against load
- One eye bolt diameter of threads or less, use two (2) nuts
- Tighten hex nut securely against load
- Minimum engagement depth is 2 x Diameter
- One eye bolt diameter of threads or less is not allowed
Machinery eye bolts must be used with great care:
- Working load limits for eye bolts are based on a straight vertical pull “in a gradually increasing manner”
- Angular pulls will significantly lower working load limits (see Shoulder Pattern) and should be avoided whenever possible
- If an angular pull is required, a properly seated Shoulder Pattern eye bolt must be used
- Loads should always be applied to eye bolts in the plane of the eye, not at an angle to this plane
- Angular pulls must never be more than a 45° pull
Loads must always be applied to eye bolts in the plane of the eye:
- Side pull in the plane of the eye.
- Sling angle must not exceed 45 °.
- Side pull out of the plane of the eye. This configuration must not be used.
Do not reeve slings between attachment points:
- Reeving introduces side pull.
- Although the upper sling angle is 60°, the resultant sling angle is 30°.
- For 1 lbf at 60° there is also a 1 lbf lateral load. The resultant load on the eye bolt is 1.73 lbf at 30°.
How should you use eye bolts safely:
- Orient the eye bolt in line with the slings. If the load is applied sideways, the eye bolt may bend.
- Pack washers between the shoulder and the load surface to ensure that the eye bolt firmly contacts the surface. Ensure that the nut is properly torqued.
- Engage at least 90% of threads in a receiving hole when using shims or washers.
- Attach only one sling leg to each eye bolt.
- Inspect and clean the eye bolt threads and the hole.
- Screw the eye bolt on all the way down and properly seat.
- Ensure the tapped hole for a screw eye bolt (body bolts) has a minimum depth of one-and-a-half times the bolt diameter.
- Install the shoulder at right angles to the axis of the hole. The shoulder should be in full contact with the surface of the object being lifted.
- Use a spreader bar with regular (non-shoulder) eye bolts to keep the lift angle at 90° to the horizontal.
- Use eye bolts at a horizontal angle greater than 45°. Sling strength at 45° is 71% of vertical sling capacity. Eye bolt strength at 45° horizontal angle drops down to 30% of vertical lifting capacity.
- Use a swivel hoist ring for angled lifts. The swivel hoist ring will adjust to any sling angle by rotating around the bolt and the hoisting eye pivots 180°.
Dangerous alterations: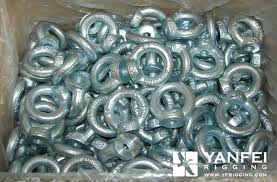
- In general, a lifting eye must never be altered by such means as grinding, machining, or cutting. Dangerous alterations of eyebolts that can contribute to catastrophic failures include:
- Machining an undercut in a shoulder lifting eye if a noncounterbore/countersunk hole is used.
- Cutting undersized threads on a blank lifting eye to make it fit.
- Welding another piece of metal to the eye or heating it in any way.
- Rapidly loading the lifting eye in shock, especially at ambient temperatures below 30 F.
- Grinding the eye to make it fit a tight space.
Machinery eye bolt Do’s:
- Visually inspect eyebolts for any damage or corrosion on threads and body
- Always be sure threads on the shank and receiving holes are clean
- Ensure the eyebolt has proper identification markings
- Always countersink receiving hole or use washers to seat the shoulder properly
- Always screw the eye bolt down completely for proper seating
- Always tighten nuts securely against the load
- When using blind tapped holes, make sure thread engagement is more than 1.5 times the diameter of the thread in steel and 2.5 times in aluminum
Machinery eye bolt Don’ts:
- Do not use the eyebolt if it is bent, damaged, or has been modified.
- Do not use if the eyebolt if it does not have proper identification markings.
- Do not use shouldered eyebolts at angles between 45 and 90 degrees to bolt the axis.
- Do not repair, replace, or modify an eyebolt.
- Do not use if a gap exists between the part and eyebolt.
- Do not use a hook larger than the diameter of the eyebolt opening.
- Do not use a plain pattern eye bolt for angular pulls
- Shock loading must be avoided.
- Never machine, grind, or cut an eye bolt.
- Never use an eye bolt that shows signs of wear or damage.
- Never use an eye bolt if theeye or shank is bent or elongated.
- Never exceed the load rating.
Examples of non-load rated eyebolts that should never be used for rigging:
Click the below link to download for rigging hardware safety check sheet and pep talk
Rigging hardwares - Safety check sheet