Lifting Safety:
Lifting equipment is any work equipment for lifting and lowering loads, and includes any accessories used in doing so (such as attachments to support, fix or anchor the equipment).
There are three key terms used in reference to the Regulations: 'lifting equipment';'lifting operations'; and 'the load'.
Examples of lifting equipment include:
- overhead cranes and their supporting runways
- patient hoists
- motor vehicle lifts
- vehicle tail lifts and cranes fitted to vehicles
- a building cleaning cradle and its suspension equipment
- goods and passenger lifts
- telehandlers and fork lifts
- lifting accessories
Lifting accessories are pieces of equipment that are used to attach the load to lifting equipment, providing a link between the two. Any lifting accessories used between lifting equipment and the load may need to be taken into account in determining the overall weight of the load.
Examples of lifting accessories include:
- fibre or rope slings
- chains (single or multiple leg)
- hooks
- eyebolts
- spreader beams
The load includes any material, people or animals (or any combination of these) that is lifted by the lifting equipment. Loads are often provided with permanent or semi-permanent fixed or attached points for lifting. In most cases, these are considered to be part of the load.
Examples of loads include:
- loose bulk materials
- sacks, bags, pallets and stillages
- discrete items (such as a large concrete block)
- machinery and any permanently attached lifting eyes
- a skip and the lugs fixed to its side
Different types of lifting equipments and its sub class :
1 ) Chain hoist.
- Liver hoists / Pull lift
- Hand chain hoise(Chain block /block and jackles)
- Electrical chain hoise
- Compressed air hoise , pneumatic chain hoist
- Hydralic chain hoist
2 ) Wire rope hoist
- Scaffold hoist
- Hand operated wire rope winches & hoist
- Electrical winches & hoist
- Over head wire rope crane hoist
- Hydralic wire rope winch/hoist
- vehicle mounted winches
- Cable pullers / Hoist
- Tractel wier rope
3 ) General Lifting equipment
- Synthetic sling
- Shackles
- Eye bolts & eye nuts
- Chain slings
- Wire rope slings
- Lifting chain
- Lifting & pulling clamps
- Runway beam mono , mono rail crane trolley
- Lifting magnet, permanant, battery electric and manual.
- Equipment identification tags
4 ) Rigging Equipment
- Cros by lifting & rigging
- Material rigging & load suspension eyes
- Lifting & rigging hooks
- Tumbuckles & rigging screws
- Wire rope accessories & fitting
- Snatch block, sheave block & crane pulley blocks.
- Load restraint equipment
- Lifting & rigging swivels.
5 ) Cranes & Ganty system
- Counter balance floor workshop cranes
- Portable garge
- Swing jib cranes
- Davit arm portable jib cranes
- Aluminium gantries
- Steel gantries
- Portable mobile swing jib cranes
- Over head cranes system
6 ) Material Handling & Jackey equipment
- Machinery, Load moving skates & material skates
- Lifting jacks
- Hydraulic Lifting Cylinders & Pumps
- Lifting beam & spreader beams
- Hand operate paller trucks
- Stacker trucks
- Genie industrials materials handling equipment
- Scrissor lift
- Gas cylinder handling equipment
- Drum Handling equipment
- Crane forks
- Platform trucks & trolley
7 ) Fork lift truck attachment
- Fork Mounted Man Riding Baskets
- Environment & Waste Handling Attachments
- Fork Lift Truck Mounted Drum Handling Attachments
- Fork Mounted Jib and Hook Attachments
- Fork Truck Scoop Attachments
- Snow Plough Fork Lift Truck Attachments
Chain Hoist :
There are three types of chain hoist. Differential, Lever Ratchet and Hand chain.
The most important thing to remember is that heavy items have mass and mass equals energy. It may not be obvious but you know if you drop something heavy on your foot it will hurt. But it may do more than hurt. An anvil, sewage block or milling vise dropped on one's foot could break numerous bones, disable and cause considerable expense.
Differential Hoists
These use a continuous loop of chain and a double chain wheel at the top with different number of pockets on the two sides. The lower "hook" wheel has grooves to ride on the chain but no pockets. As the chain is pulled around the inner load loop gets smaller or larger by the difference in the number of pockets on the chain wheel (the differential). As the lifting loop gets shorter the hand loop gets longer and vise versa. This is a bit of an inconvenience but the mechanism is as simple as they get.
Lever Ratchet Hoists
These are small portable units with capacities up to 5 tons but the common ones are rated 1/2 or 1 ton. The ratchet handle operates simple gears that pull a short load chain. The load is supported by a disk type friction brake similar to an automotive clutch disk held by a paw and sprocket (ratchet). Lifting rotates the brake/clutch on the ratchet. Lowering releases the pressure on the brake via a multi-lead screw similar to a brake Bendix.
Hand Chain Hoists (standard chain hoists)
These operate like the ratchet hoists above except a chain wheel and loop of hand chain turns the gearing. A brake holds the load and a ratchet prevents the brake from rotating one direction. The chainwheel rides on a screw that loosens the brake when the chain is pulled in the lowering direction. Most have planetary gearing on the brake wheel. Chain hoists are made with straight pulls and compound pulls up to 10 tons or more. Chain hoist are made in steel, portable aluminium housings, spark proof materials and corrosion resistant materials.
Common Features and Problems
- High quality hoists have ball thrust bearings in the hook to allow rotating the load.
- Load hooks have openings parallel to the back. Properly rated load hooks that have been overloaded will spring open and not be parallel.
- The brakes in industrial duty hoists are large and sufficient to support the load. A two ton hoist has an 8" to 10" diameter brake. Small import 2 ton hoists have small 3 to 4 inch brakes that are patently dangerous. They will slip under partial load without operation then due to heat rapidly slip more. These are dangerous junk that have no place in a safe shop.
Hoist Maintenance and Inspection
Chain hoists are durable and long lasting. The only regular maintenance is inspection, cleaning and lubricating. Chains should be kept clean and rust free. There are only a few bearing points that require oiling but these often require dismantling the hoist. Depending the use this should be done once a year or two. Since these devices have gears it is important to keep them sand and grit free. To clean the gears requires dismantling. Afterwards they should be greased with a tacky high pressure lube like Never Seize or gear grease.
Hoists that slip should be tagged "out of order" and repaired if possible. If not they should be scrapped. Chains that are worn, kinked or stretched should be replaced. Load chains have gently curved sides that when overloaded become straight and sometimes stiff to flex. Stretched, straightened chains should be scraped and replaced. Load chains on hoists that have been stretched will not run smoothly on their blocks. Snapping or popping chains are an indication of overloaded chains.
Annual Inspection:
The Annual inspection may be performed with the hoist in its normal location and do not require the hoist to be dismantled. Covers and other items normally supplied to allow inspection of components should be opened or removed for these inspections.
Inspection Items
1.Operating mechanisms checked for maladjustment and listened to for unusual sounds that may indicate problems.
2.Tightness of bolts, nuts, and rivets.
3.Excessive wear, corrosion, cracks, or distorted parts in the following:
-
load blocks
-
suspension housings
-
hand chain wheels
-
chain attachments
-
clevises
-
yokes
-
suspension bolts
-
shafts
-
gears
-
bearings
-
pins
-
rollers
-
locking and clamping devices
4. Damage or excessive wear on hook-retaining nuts or collars and pins and welds or rivets used to secure the retaining members.
5. Excessive wear or damage on load sprockets, idler sprockets, hand chain wheel, and drums or sheaves shall be checked for damage or excessive wear.
6. Hand chain-operated hoists checked for evidence of worn, glazed, or oil-contaminated friction disks; worn pawls, cams, or ratchets; and corroded, stretched, or broken pawl springs in braking mechanism.
7. Evidence of damage to supporting structure or trolley.
8. Presence of legible warning labels . 9. End connections load chains shall be checked for evidence of wear, corrosion, cracks, damage, or distortion.
10. Welded link hoist chain .
11. Hooks
Safety Factors and Testing
Traditional European and North American load lifting equipment has always had significant safety factors. Most steel crane and hoist parts are rated to be loaded to a maximum of 10,000 PSI at 1.5 to 2 times the rated load. This allows almost all parts to be safely made of mild steel. But then the parts are often made of steels that have five to ten times the strength of mild steel thus having huge safety factors. These 15 to 20 to one safety factors are what allows load lifting equipment to snag or catch a dropping load and safely absorb the inertia of such over loading.
These safety factors should never be assumed or taken advantage of. The basic 1.5 rating is the amount of test load that is periodically put on industrial cranes to test them. Private owners and small shops should also periodically inspect and test their equipment to full or 1.5x capacity and record the test.
On our large 10 Ton crane a 30,000 pound test load was not often available but occasionally we would have large assemblies that we normally did not lift. We would take advantage of these occasions and carefully lift them a few inches, have folks in the shop witness the lift then carefully put the load down. One thing we would have to be wary of was that at test load conditions the crane bridge would deflect more than that 1/4" or less and the trolley would try to roll to the center of the beam.
The above applies to real honest industrial duty equipment. There is a LOT of imported junk on the market sold by the big discount tool houses. Many of these items have ZERO safety factor and are based on ultimate failure values rather than conservative engineering values. This means they break or fail without warning if overloaded. I've seen popular "2 ton" Taiwanese hoists that had chains 1/5th the size of American hoists with load brakes that could not support half the devices rated load. I've seen many hydraulic presses with frames advertising 30 TON capacity sporting 20 ton jacks that were clearly bent from overloading. I've also seen shop floor cranes with bent arms and faulty hydraulic cylinder valves that were difficult or nearly impossible to gently lower a load. None of these devices are built to conventional safety standards. They will not withstand common load tests and should be avoided at all costs.
Hanging Hoists
Hoists can be hung statically using a loop of chain or shackle. Movable hoists are hung on a trolley. In either case the support method should be rated for the capacity of the hoist.
Trolleys should be hung on an appropriate beam. Crane or hoist beams are rated by deflection. Deflection should be 1/4" or less at the middle of the beam when fully loaded. This rule does two things. At 1/4" deflection trolleys do not roll down hill. At 1/4" deflection the strain on most beams is well within a safe range.
Calculating deflection can be daunting if you do not know how. You start with the beam specification (type, size, weight per unit length). Then look up the section modulas and plug it into the equations. Engineering handbooks have some of the data, the AISC Steel Construction manual has data on almost all beams as well as deflection formulas. Some engineering programs have the information as well.
One thing to remember about deflection is that it increases by the cube of the increase in length. So the span of the beam makes a huge difference.
Hanging hoists from wood is difficult to rate. Hanging hoists from roof trusses can be rated roughly by the roof rating but is NOT included in codes and this is NOT an engineering recommendation. Use at your own risk!
Low load utility building roofs are rated as low as 10 to 20 pounds per square foot. Standard structures are usually rated 30 to 40 pounds per square foot. Only in high snow load areas are roofs rated 50 to 50 pounds or more. If you take the area supported by a pair of trusses, say 20 by 4 feet, this is 80 square feet. Multiply by 20 and you have 1600 pounds. This is the total load those trusses may be expected to support including wind and snow. Add a third truss and you have 2400 pounds, a forth and its 3200 pounds. Your hoisting load should never be more than 50% of the rated load.
If you are hanging a shop monorail from wooden trusses the lower joist should be doubled up for at least 50% of the span or more. Gluing, nailing and bolting is recommended. A wooden beam in the trusses above the crane rail can help spread the load and add strength to the whole. If you are hanging a short steel beam a longer wood beam will help spread the load across more trusses. A bridge truss perpendicular to the roof trusses will increase the roof strength as well as spread the load.
The following are the different types of chain hoist
Ratchet lever hoists
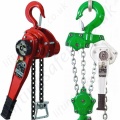
Hand chain hoist
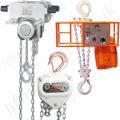
Electrical chain hoist
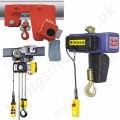
Compressed air hoist
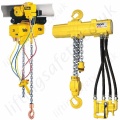
Hydraulic chain hoist
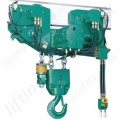
Wire rope hoist:
Available wide choice of hoists which can either lift or pull a load by means of a wire rope. There are two main differences with wire rope devices, some are designed to lift and pull (hoists) and some are designed just to pull (winches). The main factor that decides if a wire rope machine can be used to lift, pull or both is the factor of safety that it required and the unit is built to; to lift a load there is a FOS (factor of safety) requirement of 5:1, whereas to pull a load the requirement on only 3:1 FOS. Options are available for manual, electric, pneumatic or hydraulic cable pulling and lifting devices. All of which have their own unique features and specifications which can make one more suitable than another.
Wire rope scaffold hoists:
Scaffolding wire rope hoists are simply wire rope hoists that are designed to be used on construction sites for lifting building materials tools and equipment from the ground level to the working area above. Lifting equipment like scaffold hoists are also referred to as builders hoists; they as basically a wire rope lifting hoist that are suitable for outdoor use and usually supplied with a bracket and claps for attachment to a scaffolding or to a scaffold tower; the bracket will cantilever out from the scaffolding on a pivot arm that rotates to allow the load once raised to swing above the working platform. There are many different brackets and fixing methods including a counterweight gantry system, this is totally free standing scaffold tower and requires no fixings or fasteners.The lifting capacity for scaffold hoists varies from 100 – 500kg.
Scaffold / builders hoists tend to be fast lifting speeds in the region of 18 metre per minute and long heights of lift up to 100 metre. When looking for a suitable scaffold hoist the key features are HOL height of lift as you need to be able to reach your working platform from the floor.
ALWAYS:
• Store and handle grip/pull machines correctly.
• Inspect the machine, rope and accessories before use and before placing into storage.
• Ensure mounting and suspension points are secure and suitable for the full loads that will be imposed.
• Ensure the machine is free to align correctly with the rope and the rope is free of any obstructions.
• Use only the correct rope supplied for the machine.
NEVER:
• Use kinked, damaged ropes or ropes with broken wires.
• Extend or force operating levers.
• Operate raising and lowering levers at the same time.
• Use grip/pull machines if the rope is twisted or trapped.
• Use grip/pull machines for man-riding applications unless they are specifically designed/adapted for that purpose.
Storing and Handling Grip/pull Machines
Never return damaged grip/pull machines, ropes etc to storage. They should be dry, clean and protected from corrosion. Rope should be carefully coiled onto a suitable drum or frame for storage, taking care to avoid any twists. Store machines and ropes on a suitable rack, not on the floor where they may be damaged.
Using Grip/pull Machines Safely
Do not use defective grip/pull machines, ropes, pulleys etc.
Check the rigging arrangement, that anchorage and suspension points are secure and adequate for the imposed loads. Ensure the correct rope is fitted and that it is not twisted or kinked. The machine must be free to align with the rope. For lifting operations do not exceed the marked SWL. The line pull must not exceed that stated for pulling applications. Only use the operating lever provided with the machine and do not extend this with tubes etc. Undue force will damage the machine or cause safety pins to shear. Do not attempt to operate the raising and lowering levers at the same time. For man-riding applications only use a machine which has been designed or specially adapted for that purpose, following the suppliers specific instructions. Additional safety equipment will be necessary.
Hand Operated Wire Rope Winches and Hoists:
How do you intend to mount the hand operated winch, floor mounted, wall mounted or as a portable wore rope hoist? When fitting, consider the handle position on the winch to ensure that it will be operable in the area to be installed and not interfere. What environment is it to be used in, do you need corrosion resistance or made from stainless steel.
A wire rope hand operated hoist is designed to primarily lift a load though it is also safe for a hoist to pull a load whereas a hand operated wire rope winch can only pull a load and never be used to lift a load. The main reason being that the factor of safety (FOS) for both types is different, for lifting the FOS is 5:1 whereas with pulling winches only 3:1 FOS is required.
Electric Winches and Hoists, AC (Mains Powered):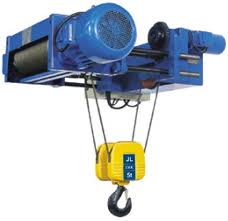
Motor - Typically the winch motor is powered by the vehicle’s battery. The motor provides power to the gear mechanism, which turns the winch drum and winds the wire rope.
- Winch Drum - The winch drum is the cylinder onto which the wire rope feeds. The drum is driven by the motor and drive train. Its direction can be changed using the remote control.
- Wire Rope - The wire rope’s diameter and length are determined by the winch’s load capacity and design. Wrapped around the winch drum and fed through the fair lead, the wire rope is looped at the end to accept the hook’s clevis pin.
- Fair lead- When using the winch at an angle, the fair lead (or wire lead) acts to guide the wire rope onto the spooling drum. It minimizes damage to the wire rope while it goes through the winch mount or bumper.
- Gear Train - The reduction gear converts the winch motor power into a large pulling force. The gear train design makes it possible for the winch to be lighter and more compact.
- Braking System - The brake is automatically applied to the winch drum when the winch motor is stopped and there is load on the wire rope. The brake prevents the winch from paying out line, which in turn holds the vehicle in place.
- Clutch - The clutch allows the operator to manually disengage the spooling drum from the gear train, enabling the drum to rotate freely (known as “free spooling”). Engaging the clutch “locks” the winch drum back onto the gear train.
- Control Box - Using electrical power from the vehicle’s battery, the control box solenoids switch power to the motor, enabling the operator to change the direction of the winch drum rotation.
- Remote Control - The remote control plugs into the winch control box, allowing the operator to control the winch direction, as well as stand well clear of the wire rope while operating the winch.
GENERAL WINCH MAINTENANCE:
Inspect the wire rope before and after each winching operation. If the wire rope has become kinked or frayed, the wire rope needs to be replaced. Be sure to also inspect the winch hook and hook pin for signs of wear or damage. Replace if necessary.
- Keep winch, wire rope, and switch control free from contaminants. Use a clean rag or towel to remove any dirt and debris. If necessary, unwind winch completely (leaving a minimum of 5 wraps on spooling drum), wipe clean, and rewind properly before storage. Using a light oil on the wire rope and winch hook can keep rust and corrosion from forming.
- Operating your winch for a long period of time places an extra burden on your vehicle’s battery. Be sure to check and maintain your battery and battery cables according to manufacturer guidelines. Also inspect switch control and all electrical connections to be certain they are clean and tight fitting.
- Inspect the remote control for damage, if so equipped. Be sure to cap the remote socket to prevent dirt and debris from entering the connections. Store remote control in a protected, clean, dry area.
- No lubrication is required for the life of the winch.
Overhead Wire Rope Crane Hoists:
Hoists can provide lifting and lowering motions in an overhead material handling system. When a hoist is mounted to a trolley on a fixed monorail, two directions of load motion are available: forward or reverse, up or down. When the hoist is mounted on a crane, three directions of load motion are available: right or left, forward or reverse, up or down. These systems can achieve straight-line moves, reduce material damage, reduce noise, minimize energy cost, reduce floor-based traffic, improve worker ergonomics, and accomplish other operational objectives.
In an overhead material handling system, hoists provide vertical movement of below-the-hook load supporting and positioning devices.
In any material handling system, the hoist is used to accurately position a load.
Types of Overhead Hoists:
- Mounting Type – There are eight suspension/mounting methods for overhead hoists: Hook Mounted, Clevis Mounted, Lug Mounted, Trolley Mounted, Deck Mounted, Base Mounted, Wall Mounted, and Ceiling Mounted.
- Lifting Medium – Four types of lifting medium for overhead hoists: Welded Link Chain, Roller Load Chain, and Wire Rope, synthetic web or rope material.
- Power Application – Three methods of applying power for overhead hoists: Manually by Hand Chain, Electric Power, and Air Power.
Hydraulic Wire Rope Winches / Hoists (Lifting and Pulling):
The Hydraulic Winch Machine has a hydraulic driving unit and is driven by a turbo charged diesel engine.The winch operates by deriving mechanical power from a turbo charged diesel engine and this power is fed to a hydraulic pump, which in turn feeds the pressurized hydraulic oil to a hydraulic motor and to the capstan unit via a planetary gear box, thereby offering a step less speed regulation. The wire rope on the drum is also laid evenly using a rope guide unit.
Application:
- Oil & Gas Industry
- Rigging & Recovery Process Industry
- Power Generation Plants
- Pipeline Fabrication Industry
- Construction Industry
- Heavy Manufacturing Industry
-
Process & Pipeline Industry
Features:
- Easy maintenance owing to open type design facilitating case of maintenance.
- Step-less speed control.
- Powerful display that shows load, speed and pulling length.
- The machine featured auto cut off function when set to designated speed/load.
- Suitable for rough conditions owing to robust construction
- Loaded with mechanical anchors.
- The machine is operated on No other electrical power is required as the controls are operating on 12 Volts DC drawn from the batter.
Wire rope hoist-scaffolding
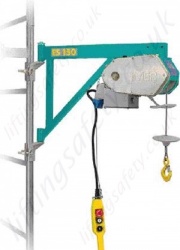
Hand operated-W&H
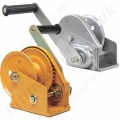
Electrical Winch & hoist
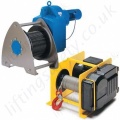
Over Head W & H
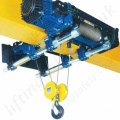
Hydraulic wire rope W & H
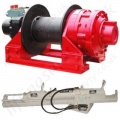
Pneumatic wire W & H
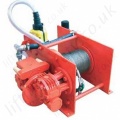
General Lifting equipment's:
Synthetic lifting slings:
Natural and synthetic fiber rope slings are used primarily for temporary work, such as construction and painting jobs, and in marine operations. Fiber rope slings are pliant, grip loads well, and do not mar the surface of the load.
The most common constructions for fiber rope slings are 3-strand laid, 8-strand plaited, and hollow braided nylon and polyester. Fiber rope slings have the following properties in common:
- Strength,
- Safety,
- Convenience,
- Load protection,
- Long life,
- Economy,
- Shock absorbency, and
- Temperature resistance.
Identification:
New slings are marked by the manufacture to show:
- The rated load for the types of hitches, and the angle upon which they are based,
- The name or trademark of the manufacturer,
- The manufacturer's code or stock number, and
- The type of material and construction.
Inspections:
This qualified person also performs additional periodic inspections where service conditions warrant, as determined on the basis of:
- Frequency of sling use,
- Severity of service conditions,
- Nature of lifts being made, and
- Experience gained during the service life of slings used in similar circumstances.
Lifting shackles -D shackles and bow:
A shackle has two main paths, the body and the pin. The body can have the anchor shape (bow) or a chain shape (D type). Each body shape can be used, depending on the specific application, with a screw pin or bolt-type pin.
- When selecting the right shackle, refer to manufacturers' tables for the safe working loads of the shackles. The rated capacity should be imprinted on the shackle and be visible.
- Shackles are sized according to the diameter of the bow section rather than the pin size. Never use a shackle if the distance between the eyes is greater than listed in the manufacturer's tables.
- Consult with the manufacturer if using shackles in extreme conditions (e.g., temperature higher than 204°C or lower than -40°C, or exposure to corrosive fumes).
inspect shackles:
- Inspect shackles regularly.
- Inspect the shackle eye and pin holes for stretching (elongation) and wear. Elongation means the metal is being overloaded.
- Inspect the shackle body for bending. A bent shackle indicates excessive side-loading.
- Inspect all shackle pins for distortion, surface blemishes, wear and fractures.
- All pins must be straight and all screw pins must be completely seated.
- Replace shackles that are bent, show excessive wear by more than 10% of the original diameter, or have an elongated eye or shackle pin holes.
Lifting Eye bolts & Eye Nuts, Lifting and Lashing Points:
Eye bolts are marked with their thread size NOT with their rated capacities. Make sure you select the correct eye bolt based on its type and capacity for the lift you are conducting.
- Use plain or regular eye bolts (non-shoulder) or ring bolts for vertical loading only. Angle loading on non-shoulder bolts will bend or break them.
- Use shoulder eye bolts for vertical or angle loading. Be aware that lifting eye bolts at an angle reduces the safe load.
- Follow the manufacturer's recommended method for angle loading.
Use eye bolts safely: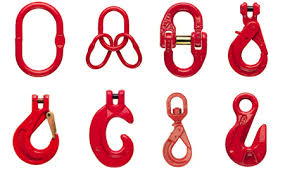
- Orient the eye bolt in line with the slings. If the load is applied sideways, the eye bolt may bend.
- Pack washers between the shoulder and the load surface to ensure that the eye bolt firmly contacts the surface. Ensure that the nut is properly torqued.
- Engage at least 90% of threads in a receiving hole when using shims or washers.
- Attach only one sling leg to each eye bolt.
- Inspect and clean the eye bolt threads and the hole.
- Screw the eye bolt on all the way down and properly seat.
- Ensure the tapped hole for a screw eye bolt (body bolts) has a minimum depth of one-and-a-half times the bolt diameter.
- Install the shoulder at right angles to the axis of the hole. The shoulder should be in full contact with the surface of the object being lifted.
- Use a spreader bar with regular (non-shoulder) eye bolts to keep the lift angle at 90° to the horizontal.
- Use eye bolts at a horizontal angle greater than 45°. Sling strength at 45° is 71% of vertical sling capacity. Eye bolt strength at 45° horizontal angle drops down to 30% of vertical lifting capacity.
- Use a swivel hoist ring for angled lifts. The swivel hoist ring will adjust to any sling angle by rotating around the bolt and the hoisting eye pivots 180°.
Chain Slings Assemblies & Components:
Alloy steel chains are often used because of their strength, durability, abrasion resistance and ability to conform to the shape of the loads on which they are used. In addition, these slings are able to lift hot materials.
Alloy steel chain slings are made from various grades of alloy, but the most common grades in use are grades 80 and 100. These chains are manufactured and tested in accordance with ASTM (American Society for Testing and Materials) guidelines. If other grades of chain are used, use them in accordance with the manufacturer's recommendations and guidance.
Identification:
New slings are marked by the manufacture to show:
- Size,
- Grade,
- The rated load, and
- Length (reach).
In addition, slings may be marked to show:
- Number of legs,
- Individual sling identification (i.e., serial number), and
- The name or trademark of the manufacturer.
Make periodic inspections of alloy steel chains slings at intervals no greater than 12 months. A good guide to follow includes:
- Yearly for normal service use,
- Monthly to quarterly for severe service use, and
- As recommended by a qualified person for special and infrequent service use.
Wire Rope Lifting Slings & Assemblies:
Wire rope is often used in slings because of its strength, durability, abrasion resistance and ability to conform to the shape of the loads on which it is used. In addition, wire rope slings are able to lift hot materials.
Wire rope used in slings can be made of ropes with either Independent Wire Rope Core (IWRC) or a fiber-core. It should be noted that a sling manufactured with a fiber-core is usually more flexible but is less resistant to environmental damage. Conversely, a core that is made of a wire rope strand tends to have greater strength and is more resistant to heat damage.
Wire rope may be manufactured using different rope lays. The lay of a wire rope describes the direction the wires and strands are twisted during the construction of the rope. Most wire rope is right lay, regular lay. This type of rope has the widest range of applications. Wire rope slings may be made of other wire rope lays at the recommendation of the sling manufacturer or a qualified person.
Wire rope slings are made from various grades of wire rope, but the most common grades in use are Extra Improved Plow Steel (EIPS) and Extra Extra Improved Plow Steel (EEIPS). These wire ropes are manufactured and tested in accordance with ASTM guidelines. If other grades of wire rope are used, use them in accordance with the manufacturer's recommendations and guidance.
When selecting a wire rope sling to give the best service, consider four characteristics: strength, ability to bend without distortion, ability to withstand abrasive wear, and ability to withstand abuse.
Lifting Clamps (Lifting & Pulling Applications):
Clamps in this category are designed for lifting application, for pulling equipment, tensioning loads and for holding items in place. Basic design styles include cam locking, screw lock clamps, scissor action lifting and suspension clamps. The main application for clamps is to handle steel plates and all types of steel profile and therefore he main lifting clamp categories include, vertical & horizontal plate clamps and beam clamps (lifting and suspension) though there are many other categories including offered in the online catalogue and these include: pulling clamps, non-marking clamps, drum handling clamps, groundworks/construction clamps, coil handling, rail and drop test clamps.
Runway Beam Monorail Crane Trolleys, Push, Geared & Electric:
With a monorail system, the hoist and trolley run on a single stationary beam. Because of their inherent speed and efficiency, monorail systems are an effective method of moving and positioning loads to specific locations. They are available in capacities up to 150 tons.
Monorails are often used for repetitive production jobs, such as paint booths and water treatment plants. Monorails are best used in applications where materials are to be transported from one fixed point to another fixed location, or through a process; e.g., painting, blasting, delivering hot metal from the furnace to a fixed pouring location. The monorail allows two axes of hook movement: up/down and forward/back along the monorail beam. There is no lateral motion under the monorail beam.
Synthetic slings
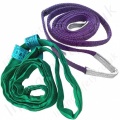
Lifting shackles
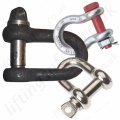
Lifting Eye bolts
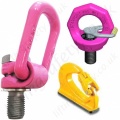
Chain Slings
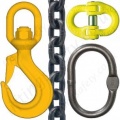
Wire Rope slings
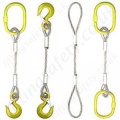
Lifting chain
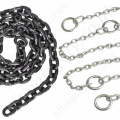
Lifting clamps
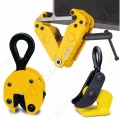
Mono rail crane
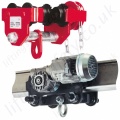
Lifting magnets
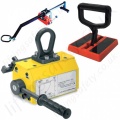
Click the below link to know download lift equipment safety check sheet & guidelines
Safety Guidelines - Electrical hoist
Safety check sheet - Hand operated hoist
Safety check sheet - Synthetic sling
Safety check sheet - Electrical chain hoist