Industrial Storage Racks safety
Introduction:
Storage racks are the most important storage solutions in an industrial manufacturing facility, as well as warehouses. They are also used in various another commercial, residential, and retail applications. Although most users know about the importance of rack safety, still it is one of the most overlooked areas.
Warehouse is a commercial building used for storing industrial goods. A warehouse houses different types of racks for storing products such as roll dispenser racks, coil racks, movable storage racks, etc. Warehouse is also an accident prone idea due to various reasons. Improper management of racks is one of the main reasons for warehouse accidents. To avoid rack related accidents, it is very important that warehouse owners maintain a safety checklist. The checklist should enlist series of tasks and activities to be undertaken by people using these racks.
Hazard Recognition:
Be aware that the following hazards may exist when using steel storage racks to store materials, equipment, machines and tools at the workplace:
- worker slips and falls from and around the racking during operations and maintenance
- overturning of the rack because of incorrect height-to-depth ratio (of the entire rack)
- failure of the racking structure because of vertical constraints, deflections, beam connections and other stability factors
- collision of moving equipment with the racking system
- overloading of the racking system if amount of product stored exceeds capacity of the racking
Hazards may also exist under the following conditions:
- improper specifications
- poor installation
- no inspection or maintenance
- improper repairs
- unknown capacity
Rack design considerations:
In order to determine the ideal storage solution, there are important safety and design considerations as follows:
- Product and Turnover
- Load Capacity
- Rack Frame and Beam Material
- Existing Facility Features
- Production Zones and Work Flow Areas
- Material Handling Equipment
- Temperature
- Code Compliance & Permitting
- Plan for Long-Term Success
- Environmental Forces
Product and Turnover:
The type of rack as well as the shelf elevations and storage bay width will, to a great degree, be
determined by your product and stock rotation requirements. How many different product will be stored? What type, size, and number of pallets will be used? How often will pallets be accessed? Do you require FIFO (first in, first out) or LIFO (last in, first out)? Will processing / picking operations require the integration of automation into your system?
Load Capacity:
Load capacity takes into account maximum pallet load, average pallet load, as well as maximum
carton load, average carton load and storage utilization factor.
Rack Frame and Beam Material
The type and configuration of your upright rack frames are determined by both the capacity they need to support and their exposure to potential impact during loading and unloading. Unlike some rack suppliers, Steel King has manufacturing facilities that specialize in both hot-rolled (structural) and roll-formed steel, so it is your racking needs that determine the type of steel that is used.
Existing Facility Features:
In addition to the floor space of your facility, take into account all features of your existingstructure – ceiling height, sprinkler systems, columns, floor drains. Be sure to account for sloping
floors within your facility, as you will be required to ensure that your rack uprights are plumb. Check your slab-on-grade capacity. Can your existing concrete floors accommodate the weight of
the system you plan to install? Do they require any special rack anchoring considerations? You will also need to map out your means-of-egress for both personnel and forklift access to ensure that maximum distances to egress are within code, especially for raised work areas.
Production Zones and Work Flow Areas:
Consider the space needed for your production work to safely occur. This is especially important
in manufacturing, where you have materials movement around equipment. For a stock and ship
operation, adequate space is required for packing, shipping, and receiving areas.
Material Handling Equipment:
The material handling equipment to be employed for the movement of the goods will impact rack
design factors. Some of the items to be considered are the type, size and number of pallets to be
used, as well as the type of fork truck vehicle being used, required aisle width, and the maximum
lift height of the truck.
Temperature:
Build your pallet racking system with temperature considerations in mind and consider the
environment where pallet racking will be used. There may be an advantage of using a particular
product based on whether the environment will be dry, in a cooler, or freezer environment.
Code Compliance & Permitting:
Rack systems may be installed only after all applicable building codes have been satisfied and
a building permit has been issued for a particular system design, geographic location, and a
particular user’s application. In most jurisdictions, the applicable building code is the legislatively adopted edition of the International Building Code (IBC) as developed, updated, and promulgated by the International Codes Council (ICC). Some localities enforce a variant of the IBC. The owner must work with the rack equipment provider to determine which code applies and to assure that their system will be designed, manufactured, and installed to satisfy all applicable requirements.
In addition to local building codes, some industries have specific code compliance requirements,
including rack capacity plaques.
Plan for Long-Term Success:
An integral part of every rack planning project is to recognize the importance of rack inspection
and maintenance.
Plan today’s system with future expansion in mind.
Environmental Forces:
Seismic design categories, along with wind and snow loads must be taken into consideration for
rack-supported structures. For free standing rack structures, adequate seismic separation must be engineered into your rack system.
According to OSHA, all goods, materials and equipment at work sites must be stacked, stored, and secured in such a way that they do not flow, move, roll, or collapse.
Storage racks are considered “building-like, non-building structures.” Therefore, according to
the International Building Code, and as reflected in the Rack Manufacturer’s Institute (RMI) Standard, racks need to be designed to the local seismic requirements, just like a building.
While all U.S. states have some potential for earthquakes, 42 of the 50 states “have a reasonable
chance of experiencing damaging ground shaking from an earthquake in 50 years,” which is
generally considered the lifetime of a building.
Types of storage racks:
Steel storage racks are universal equipment found in many workplaces. In most workplaces, they are loaded and unloaded with powered mobile equipment. Due to the common use of the phrase "storage racks" that describes all types of storage systems, as well as shelving units, this guideline provides further clarification and examples of the types of storage rack.
Types of steel storage racks:
- Selective Rack
- Drive-In Rack
- Cantilever Rack
- Over dock Storage Rack
- Die Rack
- High Capacity Wire Reel Rack
- A-Frame Vertical Storage Racks
Selective Rack
The most popular type of rack is Selective Rack, so called because it allows easy selection,
normally by service (truck) aisles. Selective Rack does not make the most complete use of floor space due to the aisles required, but may be the ideal solution for many companies. These systems can increase storage density with the integration of gravity-flow tracks, pushback carts, or double-reach application, allowing for deeper storage and less aisle space. Selective pallet racking is a popular and effective storage method in warehouses, manufacturing facilities and distribution centers due in large part to its ease of design and implementation.
Drive-In Rack
A Drive-In Rack, on the other hand, increases density and is
often utilized where group pallet selection is more likely than
individual pallet selection. With Drive-in Rack, loading and
unloading within a bay must be done from the same aisle. A similar system called Drive-Thru Rack permits loading and
unloading from both ends of a bay.
Cantilever Rack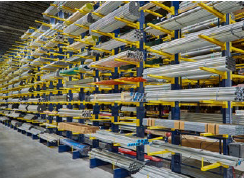
Cantilever Rack is primarily utilized to store bulk items such as
building materials (lumber, pipe, drywall, etc.) and furniture. It is commonly found in home centers and furniture warehouses.
Cantilever Rack is easily identified by the arms protruding from
the face of the columns.
Over dock Storage Rack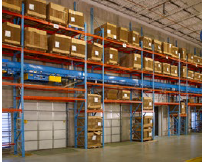
Empty pallets cluttered around loading docks are a common
warehouse problem, which can lead to operational inefficiency
and safety issues. Steel King’s Over dock Storage Rack helps solve these problems by storing your empty pallets in racking, above your loading docks. Steel King’s standard SK2000 or SK3000 racking can be designed and configured to fit around your loading dock doors.
Die Rack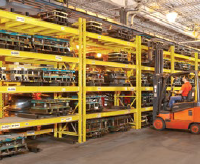
Steel die storage racks are perfect for storing dies, motors, jigs,
fixtures, and other heavy material. Standard Steel die racks
feature a solid metal shelf design allowing die placement anywhere along the shelf, and can accommodate a variety of die sizes. Shelf design allows dies to be slid on or off a shelf for easy access and storage. For optimal storage flexibility, shelves on tubular structural rack can be designed so that they are removable from the uprights and the heights adjustable in 3” increments across the entire vertical height of the upright.
High Capacity Wire Reel Rack
High capacity, wire reel racks are custom designed with the
flexibility to accommodate the size and capacity of your spools and axle brackets.
A-Frame Vertical Storage Racks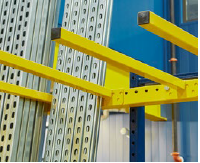
Steel King A-Frame storage racks are ideal for storing hand loaded, long slender shaped material, such as moldings, trims, lumber, ladders and gutters. These racks incorporate a unique framework, utilizing boltless pallet rack columns. Columns are angled back to create a framework that supports your material evenly and frequently all along its length.
Rack Terminology:
Six-Step Pallet Rack Design:
To determine pallet rack configurations:
1. Find the depth and width of your pallet.
2. Determine the load depth, load width, load height and weight of your largest load. For the overall height, add the height of the load and the height of the pallet together.
3. To determine front-to-back depth of your uprights, subtract 6” from your pallet depth.
Example: Your pallet is 40” Wide x 48” Long (Depth).
Subtract (48” - 6”) = 42” Uprights
4. Determine the beam width (assumes 2 pallets per beam): Multiply the load width x 2 & add 12”.
Example: Your load width is 42”: 2 x 42” = 84”+ 12” = 96” beam length.
If required, round the length up to the next highest beam length.
5. Check the beam capacity to ensure the specified beams will carry the planned load. Do not exceed beam capacity.
6. Calculate your upright height (for a system using 4” beams):
(A) Multiply the number of pallets high stored minus one pallet x 10”.
Example: If storing 4 pallets high:
4 pallets high minus one pallet is 3, then multiply 3 pallets x 10” = 30”
(B) Multiply the number of pallets high stored minus one pallet by the overall load height. Include the pallet height in the overall load height.
Example: If storing 4 pallets high, with an overall load height of 50”:
4 pallets high minus one pallet is 3, then multiply 3 pallets x 50” = 150”.
(C) Add the two numbers you solved for together (30” + 150” = 180” in this case).
This number is your upright height. See table for standard upright sizes.
Notes on Upright Height
- The vertical space between pallets allows for the beam height, and also vertical clearance to lift and remove the pallet.
- Be certain there is adequate space left between load height of uppermost pallet and
sprinkler heads, light fixtures, and other obstructions that may exist overhead.
Storage Utilization Factor(SUF):
Cube utilization is an industry term that refers to the amount of the total available space that is actually utilized, expressed as a percentage. When a space is completely filled with product, the cube utilization is 100 percent. This term is often used to describe a trailer when no more product can fit in it.
However, the reality is that as your utilization nears 100 percent, productivity within that space begins to fall – there is no room to effectively move and arrange product. The goal is to determine the optimal Storage Utilization Factor (SUF) that can provide for both fluctuations in inventory balances and honeycombing. Each type of storage – bulk, select rack, double-deep rack – has a different SUF that must be accounted for in the design of a storage system.
Extra Spaces for Inventory
Part of the SUF allowance is to provide extra storage spaces above the normal or planned inventory levels. A distribution center cannot operate efficiently if 100% of the pallet storage slots are occupied. Lift truck operators lose productivity when they must search for an available slot or consolidate partial pallets of the same stock-keeping unit (SKU) to create an empty storage slot. “Effective Utilization” is the level of storage that can be maintained as a percent of total capacity without degrading productivity and throughput.
Extra Spaces for Honeycombing
The second part of SUF is providing empty spaces for “honeycombing,” the term for partially filled pallet slots. For example, if there is one carton left on a pallet in a particular storage location, that location is not readily available to store other pallet. And while pallets can be consolidated, this takes extra time and reduces productivity. For this reason, leaving a certain percentage of empty positions actually increases efficiency.
Recommended Utilization Factors
For single-deep pallet rack storage, Steel King recommends planning for no more than 90% utilization at peak inventory levels. However, the storage utilization factor varies from one type of rack to another.
The SUF for the most common types of storage is in the chart below.
Storage Utilization Recommendation
Rack and Floor Layout:
Create a layout of the proposed racking system and total floor area used before installing steel storage racks at the workplace. This helps ensure adequate clearance and working space for safe movement and storage of materials.
Plan and Elevation Drawings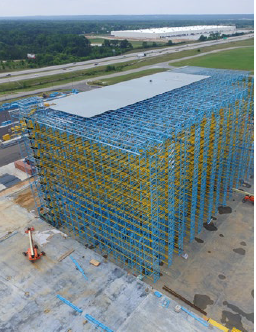
Plan and elevation drawings should include:
- dimensions for all parts of the rack system
- right-angle stacking and intersecting aisle requirements
- building clearances (including all mechanical systems)
- reference to a specific location within the building
Drawings should identify loads on buildings or structures from the racking system.
Note: The building or structure must be able to support loads imposed on it by the racking system.
Changes to rack configurations may change their capacity to handle loads. Before making any changes, consult a professional engineer or the rack manufacturer.
Rack Layout
Rack layouts should consider interaction with the building and building system, the material handling equipment, productivity issues and damage issues.
Provide adequate clearances for the following:
- between pallets; between pallets and frames (side clearances)
- between pallets and the underside of beams (lift off clearance)
- pallet overhang (loads over pallets and pallets over beams)
- forklift operations
- clearance for lift trucks or other powered mobile equipment to pass each
other in the aisles, if applicable - access to doors
All rack columns must be equipped with appropriate base plates. Proper base plates provide uniform transfer of the column load to the floor. The rack manufacturer or designer can supply data on the size and pressure exerted under the bearing plates for each type of upright and setup. This will confirm whether the floor can withstand the anticipated load. (Figures 1a and 1b illustrate types of base plates.)
Base Plate Design
A base plate must provide for anchorage and be designed to support the entire profile of the column placed on it.
The base plate must transfer the column load in a uniform manner to the supporting structure (floor).
Vertical Constraints
Rack capacity and rating depends on plumb or vertically straight rack installation. Install the vertical parts of the racks according to design specifications. Maximum tolerance is 12.5 mm per 3 m of height (1/2 in. per 10 ft. of height). A rack not installed and maintained plumb is subject to
stresses that will reduce capacity and stability.
Overturning
The height-to-depth ratio of the entire rack should not exceed 3:1 measured from the floor to the top of the rack unless the rack is suitably anchored, externally braced or properly secured to the building structure. Placing racks back to back and connecting them will increase their stability. Figure 2 illustrates the height-to depth ratio.
Deflections
At maximum working load, the deflection of rack beams must not exceed 1/180th of the span of the beam. For example, if the span of the beam is 4 m (13.12 ft.), the maximum deflection allowed is 22 mm (.87 in).
Bracing
Diagonal bracing of the racking systems depends on design considerations and varies from one racking system to another. Diagonal bracing must ensure the stability of the columns. Review the original design specifications to determine proper structure bracing.
Floors
Racks installed on uneven floors must be levelled. The columns must meet the vertical constraint standards described above and all shelves must be level.
Beam Connections
In addition to design load specifications, beams must have support connections that are capable of withstanding an upward force of 4,500 kN (1,011 lbs. of force) per connection, without failure. This protects support connections in the event that a forklift (or other powered mobile equipment)
collides with the structure.
Building Connections
Rack connections made to the building must ensure that the loads imposed by the racks do not affect the structural integrity of the building. The opposite is true also. The building should not damage the rack. This can occur if the rack attaches to the roof of a building and the roof deflects under a snow or rain load, causing deflection of the rack.
Safe Loading Conditions of the Building
Employers are responsible to ensure that safe loading conditions for a permanent or temporary building or structure (as specified in the Manitoba Building Code or the design specifications of a professional engineer), are not exceeded during its construction and, when it is used to store materials, equipment, machines or tools, as specified in Part 7 section 7.2(1) of the
workplace safety and health regulation.
Furthermore, Part 7, section 7.2(2) states: “If it appears that the loading conditions specified in subsection (1) may be exceeded when the use of a building or structure is changed, the employer must ensure that the loading conditions respecting the changed use are certified in advance of the change in use as being safe by a professional engineer. “
Rating Plates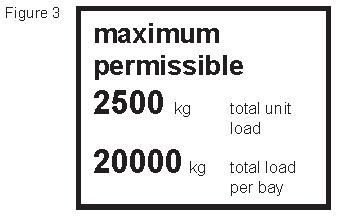
Maximum load plates must be clearly posted in a visible location at the worksite indicating allowable unit loads (ex: maximum pallet weights, sizes, etc.) and total bay loads for each type of racking. Figure 3 illustrates a sample load plate.
Type of Bolts
Anchor bolts must withstand forces caused by vertical and horizontal loading. Structurally rated bolts should be used for anchoring. Expandable bolts attaching bearing plates to concrete should be rated to secure storage racks loaded at maximum capacity safely.
Drive-in Racks
Drive-in and drive-thru rack systems are efficient ways to store large quantities of similar loads by allowing the forklift driver to enter the rack system and place the load on structural rails. A major difference between these two systems is that drive-thru racks can provide first-in/first out (FIFO)
storage, while drive-in racks only function as first-in/last out (FILO) systems.
The design of the drive-in and drive-thru racks requires much the same information as for standard pallet racks. Detailed specifications of forklifts used are needed because the rack bay opening and first tier must provide space for the lift truck and the pallet load. Specific guidelines for this type of rack are as follows:
- Racks without pallet guides – the gap between the inside edges of the opposing rails must not exceed the pallet width minus 25 mm (1 in.). See Figure 4a.
- Racks with pallet guides – the distance between the guide and inside edge of the opposite rail must not exceed the pallet width minus 19 mm (3/4 in.). See Figure 4b.
Both requirements must allow for lateral deflections that may occur under load.
Collision Protection
It is difficult to design a rack to be collision-proof, but suitable protection can be provided. Serious structural damage usually occurs when the bottom portions of exposed rack columns are struck by forklifts or other moving equipment.
Two ways recommended to protect against collision:
1. Reinforce the exposed column. See Figure 5.
2. Connect a post or guardrail to the floor to absorb any impact. See Figure 6.
Lighting
Proper lighting is important. It can make rack entry and material placement easier and help reduce rack damage.
Inspection and Maintenance:
Inspection Program
Owners or employers using steel storage racks in the workplace must ensure program is in place to inspect them regularly. The person conducting inspections should be provided with a current layout, elevation drawings and manufacturer’s instructions for the storage racks.
The inspection must identify any variance from the layout and elevation drawings provided, as well as any structural damage and missing or moved storage rack parts.
The inspection must also make note of poor operating practices, if they are observed in connection with storage racks. A record of each inspection must be kept at the workplace and a copy must
be provided to the safety and health committee or representative at the workplace. Inspection programs will be specific to each workplace and based on the size and use of each storage rack installation.
Frequency of Inspection
Experienced personnel should visually inspect heavily used racks daily. All connections must be inspected to ensure that bolts and other structural pieces are not loose or damaged.
Damaged Racks
Ninety percent of rack damage occurs between the floor and the first horizontal beam. Repairs will vary by rack system. Always consult the manufacturer about how to repair damaged racks and components properly. Conditions that contribute to rack damage:
- overloading by placing too much material on the rack
- using minimum rather than recommended material handling equipment clearances
- person placing load on the rack is inexperienced
- use of certain types of material handling equipment (ex: forklifts)
Damage Identification and Classification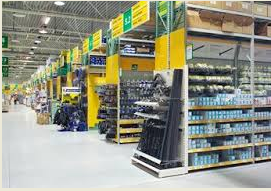
Rack damage should be identified and classified as severe structural damage or moderate damage.
- severe structural damage – refers to parts that are buckled or severely bent and must be replaced.
- moderate damage – refers to columns that are dented, slightly skewed, etc. They may be repaired by adding braces or splices strong enough to carry the intended load.
- If a part of the rack is determined unsafe, the part must be clearly identified by marking or tagging.
- Any loads in the area of the unsafe part must be immediately removed from the rack and not reloaded until repairs are complete
Repairs and Corrective Actions
Minor damage to storage racks must be repaired or replaced immediately. If storage racks receive severe or structural damage, repair work must be approved by a professional engineer. Repetitive damage, particularly to the lower section of frame columns, suggests a need for post guards, changes to the rack layout or changes to operating practices at the workplace.
5 Simple Tips to Prevent Industrial Rack Damage
Storage racks are essential and are used in almost every industry, especially in warehouses. No matter what kind of industrial storage you prefer for your facility, safety is always a top priority when it comes to protecting your inventory or storage racks. It cannot be overlooked or compromised upon. If your storage racks are not of the appropriate material or get excessively loaded, they may collapse and cause damage to the property and risk the life of workers. Here are some tips that may help prevent your storage racks from damage or failure.
Prevent Storage Rack Damage with These 5 Simple Safety Tips
If you want to avoid any racks-related disaster at your facility then consider these five essential prevention tips.
1. Choose Appropriate Racks: There are different types of racks available in the market, from selective to high-density ones. You have to choose an appropriate rack for your facility as per your requirements. Proper analysis of the rack design against your load requirement will help ensure that your storage system meets all the safety standards. Selection of the storage racks depends on various factors such as the number of units being stored in the rack, material handling method, and the area in which you are using it. It’s not enough to simply consider the weight and dimensions of the product or how the loads are configured on the rack. You also need to consider how fast your product turns or how frequently you need to take it off the shelf. For instance, a warehouse with a higher inventory turnover will require more durable racking system than a lower turnover warehouse. More to this consideration, the storage racks should meet the seismic requirements of the area in which it is located.
2. Provide Proper Space: Proper space planning and placement play an important role in storage rack usage. So, it is important that your warehouse offers wide enough space for workers to safely pass the units and complete their loading tasks effectively. Also, instruct your workers to keep aisle or corridor ways free of improperly stored items.
3. Install Protecting Guards: This is one of the important aspects when it comes to storage rack safety. Installing protective guarding is helpful in protecting both your inventory as well as workers. Even if you installed safety guards, make sure to guide or train your workers on their usage and monitor them for potential damage.
4. Maintain Usage and Training Program: One of the easiest ways to prevent your storage racks from damage is to train your workers on how to properly or safely load as well as remove the items from racks. The proper training program will help to perform the task more efficiently than ever.
5.Proper Inspections for Damage: The storage racks are damaged due to a number of causes such as loading method, the weight of the items being stored, and so on. So, it is important to inspect your rack as well as attached guard panel, and replace or repair them as needed. Conducting regular inspections help identify potential damage before it becomes a costly issue. Also, repairing work might hassle you, but it’s still faster as well as economical than replacing entire storage racks.
Tips for Warehouse Rack Safety
Warehouse is a commercial building used for storing industrial goods. A warehouse houses different types of racks for storing products such as roll dispenser racks, coil racks, movable storage racks, etc. Warehouse is also an accident prone idea due to various reasons. Improper management of racks is one of the main reasons for warehouse accidents. To avoid rack related accidents, it is very important that warehouse owners maintain a safety checklist. The checklist should enlist series of tasks and activities to be undertaken by people using these racks. This post concentrates on a checklist of tips, which will help the warehouse managers, working staff, and lift operators to ensure their safety.
4 Tips to Keep Away Your Warehouse Rack Woes
Below are the five tips, which will help a warehouse owner or workers realize value for storage racks.
- Avoid Overloading of Racks: Warehouse racks have twice load bearing capacities than other commercial racks. But it is advised not to overload these racks because they are engineered for static loads, not for lateral loads. Hence, it is important to read the specification label mentioned on the rack for understanding its load bearing capacity. Generally, manufacturers add labels on the racks, which help users to understand dimensions and specifications of the rack. It is always assumed that weight on the rack is evenly distributed across it. The basic science behind loading the rack is ensuring heavy loads are placed on one side, with the lighter loads on the other side. This ensures an effective storage solution and helps prevent accidents that may occur due to over loading.
- Ask for the Replacement Labels: Labels on various warehouse racks such as coils racks or roll dispenser racks are sturdy, and may last long. At times, the labels may be scratched off due to daily abuse. As, these labels are critical because they provide the specification of the rack to the workers. Hence, warehouse owner should take necessary steps to replace scratched labels as soon as they notice them.
- Avoid Damaged Racks: Many times, warehouse owners overlook faulty bases, and other minor damages. However, these minor issues aggravate in the long run, and endanger lives of people using these racks. Hence, it is always advisable to conduct timely repairs, as soon as minor defects are noticed. Also, as per the safety guidelines, the racks that are severely damaged must be disposed at the earliest. This will help prevent accidents that may occur due to their collapsing or disintegration.
- Don’t Tamper with Rack Components: Any kind of tampering in the form of drilling holes, grinding or cutting through the warehouse racks should be avoided. It is always advisable to approach the manufacturer or expert engineer for any kind of changes to be made. An expert intervention in this matter will ensure long term performance of these racks.
Click the below link to know detail about warehouse design presentation and pallet rack inspection check sheet
Power point presentation - Warehouse Design
Safety check sheet - Pallet rack inspection