Chemical Safety :
What are chemical substances: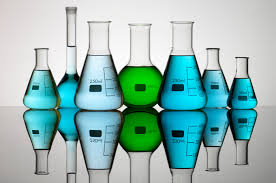
A chemical substance is a material with a specific chemical composition.Water is an example of a chemical substance - it always has the same number of hydrogen and oxygen (e.g. H2O). Some everyday chemicals include cleaning materials, cosmetics, plastics, paint,dyestuffs, sugar, solvents, etc. A chemical substance can exist as a solid, liquid or gas and still be the same substance. For example, water and steam are different forms of the same substance.
Form of chemicals:
Chemicals are present in every workplace. Even in the cleanest, most modern office, employees
may be routinely exposed to inks, toners and adhesives not to mention a wide range of chemicals
used in cleaning and maintenance.
Chemicals can exist in many forms:
- Dust, fumes, fibres, powders.
- Liquids.
- Gases, vapours, mists.
Any chemical, in either gas, liquid or solid form, that has the potential to cause harm is referred to asa hazardous or dangerous chemical. Such chemicals include those:
- Brought directly into the workplace and handled, stored and used for processing e.g.
solvents, cleaning agents, glues, resins, paints.
- Generated by a process or work activity e.g. fumes from welding/ soldering, dust from
machining of wood, flour dust, solvents.
- Generated as waste or residue e.g. fumes from soldering iron, carbon monoxide from
engine or motor exhausts.
Chemicals be hazardous to health:
Chemicals can cause many different types of harm, ranging from mild skin irritation to cancer. The
effects of hazardous chemicals may be seen:
- Chronic:Immediately after contact (e.g. chemical burn) or many years after the exposure (e.g. lung cancer following exposure to asbestos).
- Acute :Following a single short exposure (e.g. infrequent use of a chemical) or longer-term exposures (e.g. daily use of a chemical in the workplace).
-
Algergy :The effect is exerted through the immune system (multiple initial doses result in sensitization with the accumulation of antibodies; subsequent low-level exposure triggers a response; pronounced individual susceptibility) e.g. respiratory and skin sensitizes (chrome, nickel, platinum salts).
Therefore, it is important to minimise exposure to chemicals at all times. In order for a chemical to be hazardous to a person’s health, it must either be in contact with or enter the body.
Risk from chemical exposure:
If the chemicals that are used in your workplace are not properly controlled, then it is possible you are being exposed to them.Whether this exposure causes you any harm depends on a combination of factors:
- how hazardous the chemical is;
- how long you are exposed to the chemical (e.g. 5 minutes, 3 hours);
- how often you are exposed (e.g. twice a week/month)
Here are some examples of how chemicals can affect the body.
Effects on brain and nervous system
For example, exposure to pesticides, mercury, lead, solvents, carbon monoxide gas.
Eye, nose and throat irritation (dryness, soreness or pain)
For example, exposure to acid mists and vapours, welding fumes or diesel exhaust.
Effects on the lung Lung damage
For example asbestos (lung cancer), welding fume (chronic obstructive pulmonary disease).
Irritant induced asthma
For example acids (“burn effect” on airways).
Allergic asthma
For example flour dust,isocyanate (in 2-pack paints), wood dust
Liver damage
For example, exposure to vinyl chloride.
Bladder damage
For example, exposure to some azo dyes (bladder cancer).
Effects on skin
Allergic contact dermatitis
For example nickel, latex, chromate (found in some cements).
Irritant contact dermatitis
For example solvents, detergents, oils, lubricants.
Effects on blood and bone marrow
For example, exposure to benzene in petrol fumes (anemia and leukaemia).
chemicals effect the body:
You have seen how chemicals effect the body. There are four ways chemicals can enter the body:
Inhalation:
Breathing in contaminated air is the most common way that workplace chemicals enterthe body.
Contact with the skin or eyes:
Some chemicals can damage the skin or eyes (e.g. irritation) or pass through the skin into the body.
Ingestion:
Workplace chemicals may be swallowed accidentally if food or hands are contaminated.
Injection:
Injection can occur when a sharp object (e.g. needle) punctures the skin and injects a
chemical directly into the bloodstream.
Health effects of exposure to chemicals:
Term What this means to you
Remember, if you are in control of your workplace or have specific responsibilities for managing
safety, then you need to ensure that you are controlling all hazards, in whatever form that chemical
may exist in the workplace.
How to find information about chemical hazards:
The most important sources of information on the hazards of your chemicals are the label and the
safety data sheet (SDS).
Labels
Chemicals should be supplied with a label attached to the container. The label gives information on the chemical or product name, the chemical hazards and the precautions you should take into account to ensure safe use.
Safety Data Sheets:
You must have a SDS for each hazardous chemical that you use. If you don’t, contact the supplier,
who is required to give you one. You should keep your SDSs in a clearly identified place where they
can be easily accessed by your employees and by emergency services - they will require these sheets when they attend a chemical incident.You should make sure all your employees know
where the SDSs are stored and that they have read and understood them, if required.
Safety data sheets must:
- Be provided for chemicals classified as hazardous.
- Contain 16 headings.
- Be prepared by a competent person.
- Be specific to the chemical.
- Be clear and understandable.
- Be provided free of charge.
- Be provided no later than at the time of first delivery.
- Be provided upon update or revision to everyone who has received the chemical during
the previous 12 months.
- Be dated and the pages numbered.
SDS:
The SDS plays a number of roles in managing the safe use of chemicals in your workplace:
- It ensures the product is being used as intended by the manufacturer or importer.
- It is a key tool for risk assessment as it includes detailed hazard information.
- It provides options for appropriate controls measures and procedures to be applied.
- Sufficient information should be provided to select the necessary Personal Protective Equipment (PPE) and to develop necessary emergency procedures.
- It may be used as the basis of a training program for workers as it covers hazards, information on safe handling and storage and emergency procedures.
- Workplace monitoring and health surveillance strategies may often be based on advice contained in the SDS.
This guide will explain which sections of the SDS you should refer to for information on the identity
of your chemicals and their hazards, in addition to advice on control measures, safe storage and
emergency measures to be followed in case of an accident.
Identified your chemical hazards?
The label and SDS are the most important sources of information about the hazardous properties
of your chemicals, so it is important that you have an up to date SDS for each chemical and that the
label attached to the chemical container is visible.
Hazard pictograms - what do they mean?
Until 2015, you will see either hazard symbols or new hazard pictograms on SDSs and labels.
The nine pictograms according to the new CLP* Regulation are presented below, along with the
existing hazard symbols which you might be familiar with. An example of the type of hazards
associated with each are shown below.
You can use the Chemical Inventory template at the back of this toolkit to record all the chemicals
you identify and their hazards.
Assessed the exposure to the chemical:
Once you have identified your chemicals and their hazards, you then need to assess what the
potential exposure to the chemical is.
An exposure assessment involves looking at each chemical which you have identified and
considering the following questions:
Assessed the risk of your chemicals:
Once you have identified your chemical hazards and considered the exposure to them, you then
need to assess the risk for each.
Assessing the risk involves:
- Evaluating the information on the hazards and uses (potential exposure) of the chemical.
- Considering the likelihood of being exposed to a hazard and the severity of that hazard, which may lead to an adverse effect on health or safety.
You can assess the risk in lots of ways; you just need to decide a scale. Here is an example of a
possible scale:
How likely is it that an exposure leading to ill-health could happen?
- High: Exposure to the chemical is likely. For example, very frequent use or use of largequantities where the possibility of exposure to skin or breathing chemical fumes is expected (e.g. cleaning up spills, welding activities with no ventilation control).
- Low: Exposure to the chemical is unlikely. For example, very small amounts used or is used infrequently and under conditions where there is little or no chance of contact (e.g. chemical is used in a closed/contained system).
How severe is the hazard?
- High:For example, serious, irreversible or potentially fatal health effects (carcinogenicity, mutagenicity, reproductive toxicity, respiratory sensitization) or serious physical chemical effects (explosion).
- Medium:For example, less serious, potentially irreversible, non-fatal health effects (e.g. skin sensitization, corrosive to skin or eye); physical chemical effects (e.g. flammable) or environmental effects (e.g. hazardous to aquatic environment).
-
Low: Slight/transient, reversible, non-fatal health effects (e.g. irritating to skin or
eyes).
There are no definitive rules as to what constitutes a high, medium or low risk. As a general rule:
Suitable control measures:
Once you have assessed the risk associated with the use of your chemicals, you then need to decide. what control measures are required to keep you, your employees and your workplace safe.
At this stage you should also consider any current control measures that are in place, such as:
- Type of engineering controls e.g. enclosures and ventilation – are they effective and maintained regularly?
- Current work practices or procedures.
- Personal protective and safety equipment.
- Training provided to employees.
- Hygiene arrangements e.g. separate meal and wash facilities.
- Storage arrangements.
- Level of housekeeping.
- Disposal of waste.
- Emergency procedures e.g. eyewash, emergency shower.
You need to decide your control strategy for each of your chemicals. The level of control that needs
to be put in place depends on the level of risk of exposure.
1. Eliminate the hazardous chemical
Remove hazardous chemicals from the process or task.
- If you are not using a hazardous chemical, then there is no risk! Eliminating the hazardous chemical is the best way to control the risk. Consider whether you really need to use a chemical at all. For example, in recent years paint manufacturers have been able to eliminate hazardous solvents such as xylene.
- You could also consider whether it is possible to use a different process which does not need a hazardous chemical.
2. Substitute with a less hazardous chemical
- Replace a hazardous chemical with a less hazardous one.
- It may be possible to replace your hazardous chemical with a less hazardous one. For example, you could replace isocyanate based paints for water based paints. You could also use a less hazardous form of the same chemical. For example, using a pellet rather than a powder form of the chemical .could have a significant effect on reducing inhalable dust levels.
- It is important that you consider the hazards and potential exposure associated with the
replacement chemical to ensure that no new hazard is introduced to the workplace.
3. Install engineering controls
An engineering control is where some piece of equipment is installed to prevent or reduce exposure.
Engineering controls aim to separate your employees from the chemical hazard by placing a physical barrier between them and the chemical.
Examples of such controls include:
- Carrying out your process in closed containers which are vented to a safe place.
- Using local exhaust ventilation (LEV) at the source of the hazard.
- Using isolation/containment hoods or booths.
A spray booth used in spray painting or a local exhaust system to remove welding fumes is an
example of an engineering control.
The correct design and installation of engineering controls which are suitable for your specific use
is crucial if it is to give you adequate control. Therefore, you may need to obtain expert advice if you
need to install engineering controls.
Administrative controls in place: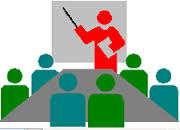
Use of management and administrative procedures to reduce or eliminate exposure.
Look how the work is done and consider how employees are exposed to the chemical. Think about
how the job could be done differently to avoid exposures.
Where it is not possible to eliminate or isolate the chemical hazard, you should minimize exposure
to it. This can be achieved by introducing procedures in your workplace to:
- Minimise the number of employees who might be involved in a task. For example implementing job rotation.
- Exclude other employees not involved in the task from the area where the chemical is being used.
- Provide training to your employees on the hazards and safe use of the chemicals they work with.
- Ensure chemicals with hazardous properties are correctly stored.
- Ensure emergency procedures are in place in the event of an accident e.g. spillage.
Training
Training needs to be well planned so that you and your employees get maximum benefit from it. It
is crucial that on completion of the training your employees fully understand:
- What the chemical hazards are.
- What the potential risks to their health could be.
- What controls are in place to protect health and safety.
- How to use, handle, move and store the chemicals in a safe manner, including proper use
of equipment (e.g. engineering controls, PPE).
- How to safely clean up spills.
- How to report a problem and who to report it to.
- What to do in an emergency.
Safe Storage of Chemicals: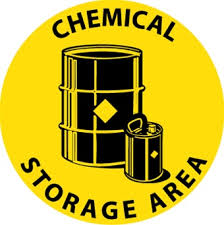
Hazardous chemicals should be stored under appropriate conditions, taking into account the
chemicals’ specific properties. Instructions on safe storage of chemicals can be found in Section 7 of the SDS.
It is also important to note if there are conditions under which hazardous reactions may occur.
For example, chemicals that can react together to form unstable or toxic products, or produce
heat, should be kept segregated. Flammable liquids stored near a heat source could result in a fire.
Section 10 of the SDS gives advice on such conditions that you should take into account when
storing your chemicals.
Chemicals known to be carcinogenic, mutagenic or toxic to reproduction should be kept under strict control.
Chemicals with typical properties and characteristics that are relevant include:
- Flammable chemicals.
- Toxic or corrosive chemicals.
- Chemicals that emit highly toxic fumes in the event of a fire.
- Chemicals which, in contact with water, give off flammable gas.
- Oxidizing chemicals.
- Explosives.
- Unstable chemicals.
- Compressed gases.
When storing chemicals you should consider:
- The compatibility of different chemicals. For example, oxidizing chemicals should be kept
separate from flammable liquids or other flammable chemicals.
- Limiting the quantities of chemicals to be stored.
- Ensuring there is adequate security of and access to storage areas. Potential ignition sources should be prohibited or controlled.
- A safe location for storage areas. In order to minimise the effects of an incident, storage areas for chemicals should be kept separate from process areas, occupied buildings and,other storage areas.
- The appropriate construction, nature and integrity of storage containers.
- Safe loading, unloading and transport around he workplace.
- Adequate precautions and procedures in case of spillage.
- Temperature, humidity and ventilation arrangements. Ventilation arrangements should ensure that there is no accumulation of gases, vapors or fumes in enclosed areas.
Personal protective equipment (PPE):
This is the last line of defence!
The use of PPE should be the last line of defense and not regarded as an alternative to other
suitable control measures which are higher up the hierarchy. It should provide adequate protection
against the risk from the hazardous chemicals to which the wearer is exposed, for the duration of
the exposure, taking into account the type of work being carried out.
In practical terms, you may have to apply a number of control measures. For example, even with
good engineering controls you may still need to examine whether administrative controls and PPE
are also needed. The further up the hierarchy you take action the better. You do not want to be in a
situation where you are highly reliant on PPE for protection from chemical hazards.
Section 8 of the SDS gives advice on steps needed to reduce exposure, including advice on
appropriate PPE. Personal protective equipment can include:
- Eye/face protection (e.g. safety glasses, goggles, face shields).
- Skin protection (e.g. chemical resistant footwear – shoes/boots/wellingtons, clothing –aprons/suits).
- Hand protection (e.g. gloves or gauntlets, disposable or otherwise, which are suitable for the job).
- Respiratory protection (e.g. respirators, masks or hoods that give adequate protection).
- Thermal protection (employees may need to be protected from excess heat or cold with appropriate clothing).
Ideally, each person should have their own equipment. They should be trained how to use it effectively, how to keep it in good condition, and where and how to store it safely to prevent
contamination.
PPE should comply with international standards i.e. be CE Marked. A CE Mark shows that the
equipment conforms with the relevant standard. PPE should be suitable for its purpose and there should be a sufficient supply available in the workplace for all employees who require it.
Where employees have been informed that PPE is required for a specific task, they should use the
equipment provided throughout the time they are exposed to the chemical hazard and supervision
should be provided to ensure that the equipment is properly used.
All personal protective equipment that is necessary for the safe use of chemicals should be
provided and maintained by the employer without cost to the employee.
CHEMICAL WARNING SIGNAGES
Ethylene Oxide explosion
Methyl Iso cyanide explosion
Click the below link to down load the chemical exposure check sheet & signage
Chemical Exposure - Safety Check sheet
Chemical storage - Safety signage
Chemical risk - Animation video